GARANT Vibratory finishing machines GMT35 and GMT2 for perfect surfaces
Vibratory finishing has huge potential
Vibratory finishing, also known as barrel finishing, is used to finish the surface of metal and plastic workpieces.
The workpieces are placed in a trough together with grinding or polishing media (grinding bodies) and an additional agent (compound) in an aqueous solution. The oscillating movement (vibratory finishing) of the container creates a relative movement between the workpiece and the media. The abrasive media, so-called grinding bodies or chips, remove the material as required. Depending on the specific requirements, the removal rate can be set higher or lower by different process parameters.
For automated finishing of small to medium batch sizes, we recommend the vibratory finishing machines from GARANT in a compact design.
GARANT GMT35 Vibratory finishing machine
GARANT GMT2 Vibratory finishing machine
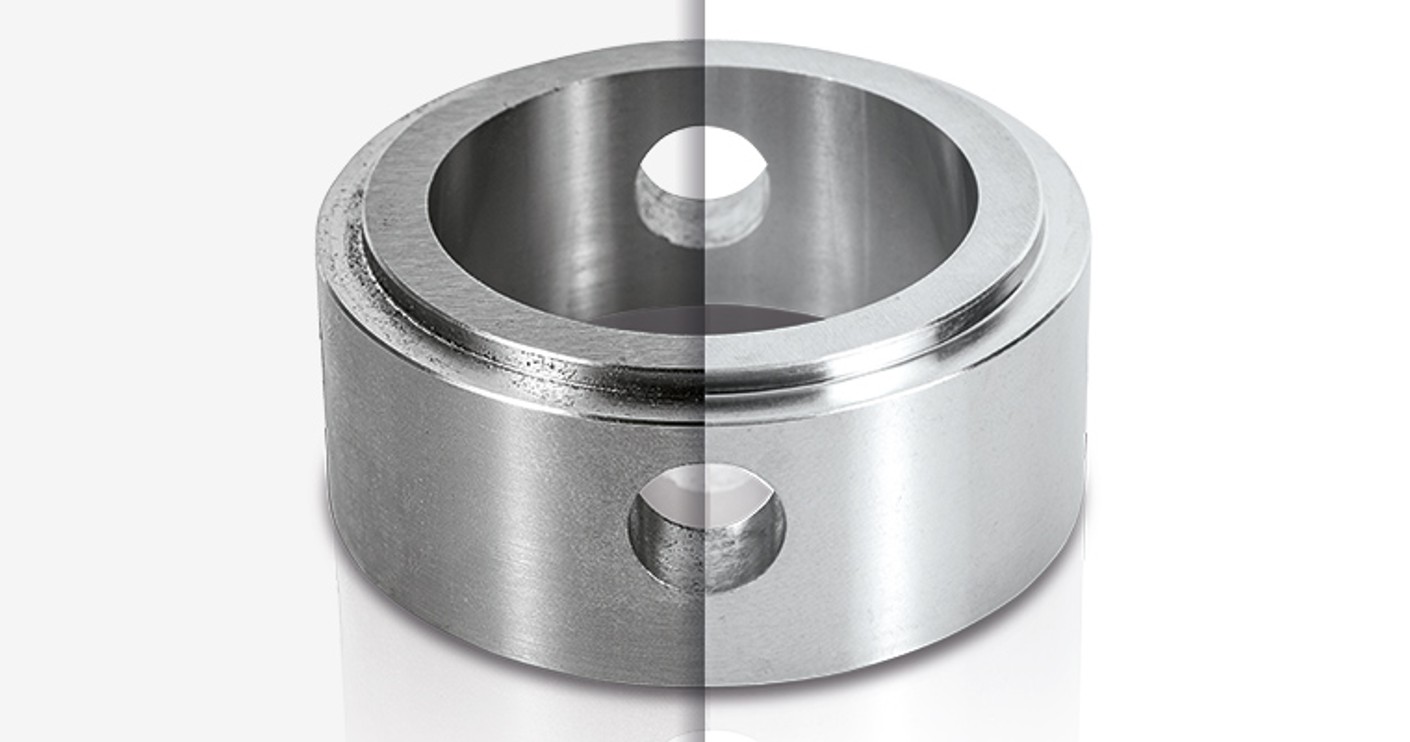
Your requirements
- High level of flexibility for the finishing process
- Small to medium batch sizes (1 – 500 pieces)
- Work in up to three shifts and process several workpieces simultaneously
- A mobile and flexible solution, without high investment costs
- No need for major maintenance and inspections
- In-house processing to retain expertise and transparency in all production steps

Your benefits
- Numerous applications: Polishing, deburring, finishing 3D printed parts and much more
- Top-quality results: Visible and measurable results
- Proximity: Located directly next to the machine, allowing you to keep an eye on things at all times
- No need to send products to external service providers: production and finishing at the same location
- Time savings: Process and production times shortened
- No need for manual processing: Shorter processing times
4 simple steps for you. A giant leap for your productivity
Our technical advisors make your entry into the world of vibratory finishing as easy as possible by providing detailed advice. Through a test machining of your components at our premises, you can clearly assess the advantages of your planned investment and receive a guideline with which you can directly start machining your workpieces after purchasing the GARANT GMT35 or GARANT GMT2.

1. Advice on site
Our specialist advisers would be happy to advise you on site, with no obligation. Here, all data is recorded and the feasibility of using our vibratory finishing solutions for your machining process with is checked. Points such as workpiece geometry, surface requirements or quantity to be produced annually are precisely analysed and recorded.

2. Feasibility check
With our customer sample part processing, we offer all customers interested in a GMT35 a service for test processing of individual components in advance. This gives you a clear picture of what you can expect from our products in the future before you buy.

3. Offer
You will receive a detailed offer containing all the products required for your future vibratory finishing process.

4. Commissioning
When the GMT35 vibratory finishing machine is delivered, our specialist consultants start up the machine together with you and give you detailed instructions on the machine.
GARANT GMT35: mobile vibratory finishing machine with integrated separating station

1. Transport trolley
- Quick and easy transport
- Three storage boxes for abrasive media and workpieces
2. Separation station
- Automatic separation of workpiece and abrasive media
- Three sieves with different hole patterns
- Easy change of abrasive media
3. Soundproofing
- Machine cladding for soundproofing with noise-absorption hood
- Inside of trough and funnel outlet lined with polyurethane
- Noise level < 80 dB
4. Controls
- Proteced against splashed water and vibrations
- Intuitive operation via touch screen
- Numerous setting options: processing time, speed, pump control, etc.
- Individual processing steps can be programmed
5. Trough vibrator
- Powerful motor
- 35 litre steel trough, inside lined (15 mm polyurethane layer)
- Trough can be divided using divider
- Constant water supply of 45 l/min via two outlets
6. Mobility
- Rollers on the underside for easy transport
- Ony 230 V connection – no compressed air or permanent water line required
- Saves space – machine with trolley measures (WxDxH) 2030 x 710 x 1380 mm
7. Integrated wastewater treatment
- Large water tank (45 litres) for wet processing
- Wastewater treatment with settling tank
GARANT GMT2: compact vibratory finishing machine with removable separating station

Compact mass finishing machine for automated finishing work on small to medium batch sizes. The preferred choice for deburring turned and milled parts and 3D-printed workpieces. Suitable for metals and plastics. This machine can also handle the subsequent step of polishing. Only dry machining is recommended (no compound required).
Properties:
- Powerful motor with defined speed range
- Steel trough (2 l) with polyurethane coating
- Removable separating station for manually separating the workpiece and grinding medium
- Effortless separation thanks to ergonomic tipping mechanism
- Intuitive control via control panel with timer function
- Quiet, dust-free working thanks to transparent cover

Ergonomic tipping mechanism for convenient separation of components

Removable separation station with stainless steel base body and two different separating sieves

Control panel with start/stop timer function. Simple control.

Recessed handle
Extensive GMT2 starter set at an attractive price
- 1 pc. vibratory finishing machine with control panel and removable separating station
- 1 pc. separating screen with 10 mm hole grid 1 pc. separating screen with 18 mm hole grid
- 1 pc. ceramic grinding bodies (3 kg), triangular, coarse (No. 501505 0606T )
- 1 pc. ceramic grinding bodies (3 kg), triangular (oblique), coarse (No. 501515 1015TA )
- 1 pc. ceramic grinding bodies (3 kg), cylinder (oblique), coarse (No. 501525 0305CA )
- 1 pc. porcelain grinding bodies (3 kg), cylinder (oblique), polishing (No. 501585 0406CA )
- 1 pc. storage box (No. 964486 EF4070 )
- 1 pc. GARANT GreenPlus Flex Cleaner 500 ml (No. 088001 500 )
- 1 pc. 3M high-performance cleaning cloth (No. 089190 BLUE
)
Everything from a single source
The right interaction between vibratory finishing machine, grinding bodies, compounds, personal protective equipment and cleaning equipment is a guarantee for optimum grinding results.
1. GARANT Vibratory finishing machines - the quick entry into automated post-processing.
2. Optimally matched grinding bodies and compounds guarantee a smooth process.
3. The right PPE and cleaning devices guarantee maximum protection. Ultrasonic cleaning afterwards.

The GARANT vibratory finishing machine GMT35 not only impresses with its high performance and mobility, but also with its sophisticated functionalities and appealing design. The jury of the German Design Award saw it the same way, as they awarded the machine as "Winner" in the category "Industry".
A simple solution for any requirement
Practical knowledge of vibratory finishing: tips and suggested solutions
Gentle cleaning without residues through ultrasound
After vibratory finishing, do you have very high requirements when it comes to cleaning and drying the components?
In this case, cleaning with ultrasonic cleaning equipment and suitable cleaning agents is recommended. The injection of ultrasound into the liquids creates a pulsating flow with a multitude of tiny bubbles of gas, which “implode” on striking a solid body. The energy thereby released “blasts” the dirt off the parts to be cleaned. Since the cleaning fluid also penetrates into holes and undercuts, ultrasound reliably cleans even complex geometries. In contrast to mechanical cleaning or cleaning with high-pressure jets, ultrasound is gentle to the surface of the components.
Discover our range of ultrasonic cleaning equipment and accessories here