Procesbetrouwbare schroefdraadproductie - productie van binnenschroefdraad
Ontdek alles wat u moet weten over de verschillende productieprocessen van interne schroefdraad
In de productietechnologie is de productie van interne schroefdraad een van de meest veeleisende bewerkingstaken.
De schroefdraad bevindt zich vaak aan het einde van een fabricageproces en is daarom bepalend voor de kwaliteit van het werkstuk. Defecte schroefdraad betekent meestal hoge extra kosten. Procesbetrouwbaarheid heeft absolute prioriteit, maar er moet ook rekening worden gehouden met korte cyclustijden en economische productieprocessen.
Hier vindt u een overzicht van de volgende draadproductieprocessen:
1. Fabricageproces: tappen
2. Fabricageproces: draadvorming
3. Fabricageproces: draadfrezen
4. Fabricageproces: boren cirkeldraad frezen
Inleiding: Basisbegrippen op het gebied van threads
Algemene aanduidingen en opmerkingen:
1. Fabricageproces: tappen

Het universele proces voor interne schroefdraad.
Tappen is het meest bekende proces voor het produceren van interne schroefdraad.
Hoge productiviteit, relatief lage kosten en universele toepassingsmogelijkheden (op conventionele gereedschapsmachines, transfersystemen, bewerkingscentra) staan hier centraal. Kranen van HSS /HSS-E /HSS-E-PM/VHM voldoen aan de eisen van de gebruiker.
Eigenaardigheden van draadproductieBij de schroefdraadproductie is er een vormpassing tussen het gereedschap en het werkstuk. Schroefdraadmaat, schroefdraadspoed en tolerantie worden nauwkeurig bepaald door de tap. Dit levert echter specifieke problemen op bij de verwerking in vergelijking met boren of frezen:
- Gecombineerde axiale en radiale bewegingen
- Het controleren van de spilspeling is noodzakelijk om geleidingsfouten te voorkomen
- Voeding en snijsnelheid zijn direct gerelateerd
Doorlopende en blinde gaten schroefdraad
Bij het selecteren van de kraan moet de vorm van de kabel zo lang mogelijk zijn. Een lange afschuining belast het gereedschap minder en de snijkantbelasting wordt verminderd. Dit aspect wordt belangrijker naarmate de materiaalsterkte toeneemt.
Doorlopende kraan
Bij deze (recht gecanneleerde) tappen met spiraalpunt wordt de spaan in de voedingsrichting naar beneden afgevoerd en valt naar beneden wanneer het gereedschap naar buiten komt. Daarom zijn deze gereedschappen niet geschikt voor blindgatbewerking. Wanneer de draairichting wordt omgekeerd (omgekeerd), wordt de gecomprimeerde chip niet afgeschoren en vastgelopen.
Bij gebruik van deze tappen voor het bewerken van blinde gaten is schade aan de schroefdraad of gereedschapsbreuk onvermijdelijk. Bij het bewerken van brosse materialen worden tappen met rechte groeven zonder spiraalpunt gebruikt. Vanwege de neiging van de brosse materialen om afbrokkelende spanen te vormen, kunnen gereedschappen van dit ontwerp worden gebruikt voor het bewerken van doorlopende gaten en voor blinde gaten.

Form A
6 - 8 pitch cut, voor korte doorlopende gaten.

Form B
4 - 5 draden met spiraalpunt, universeel voor doorlopende gaten

Form D
4 - 5 schroefdraad, voor doorlopende of blinde gaten
Blind gat kraan
Over het algemeen stelt de productie van een blindgatschroefdraad hogere eisen aan het gereedschap. De spanen moeten via de spaangoot naar boven worden getransporteerd. Bij het omkeren en afschuiven van de spaanwortel werken hoge torsiekrachten op de tap.

Form D
4 - 5 spoed lood, voor blinde gaten met een lange schroefdraadloop.

Form C
2 - 3 gangen knippen, voor universeel gebruik.

Form E
1,5 - 2 omwentelingen eerste snede, korte schroefdraaduitloop voor de grootst mogelijke schroefdraaddieptes.
Voor- en nadelen van tappen

Voordelen:
- Breed scala aan toepassingen in bijna alle materialen
- Geen speciale eisen aan de machine
- Indien nodig kan de schroefdraad met hetzelfde gereedschap worden bijgesneden
- Handmatig gebruik is in principe mogelijk
- Meestal goedkope oplossing voor draadproductie

Nadelen:
- Spaanafvoer veroorzaakt vaak problemen
- Procesonzekerheid door vorming van spaanders
- Gereedschapsbreuk leidt meestal tot uitval
Foutpreventie bij tappen
Indeling in prestatiecategorieën
Voor een gemakkelijke en correcte productkeuze zijn onze kranen onderverdeeld in groepen:
Onze GARANT highlight-producten voor tappen:
2. Fabricageproces: schroefdraadvorming

Bij draadvormen wordt de schroefdraad gemaakt door koudvormen, spaanvorming en spaanafvoer worden geëlimineerd. Dit voordeel betekent dat de draadvormer betrouwbaar kan worden gebruikt voor blinde en doorlopende schroefdraad, zelfs bij kritische L×D-verhoudingen van meer dan 4×D schroefdraaddiepte.
Spanningsfasen in het draadvormingsproces
De koppelbelasting op het gereedschap is tot 30% hoger bij draadvormen in vergelijking met tappen. Aangezien een draadvormer geen spaankamers nodig heeft voor spaanafvoer, kan de kerndiameter van het gereedschap stabieler worden ontworpen. Hierdoor kan een draadvormer ook bij de hoogste eisen betrouwbaar worden gebruikt.
De volgende factoren hebben de grootste invloed op de koppelontwikkeling:
- Werkstuk materiaal
- Voorboor diameter
- Draad
- Smering
- Coating en geometrie
Om de torsiekrachten zo laag mogelijk te houden, moeten de optimale kerngatdiameter en een hoogwaardig smeermiddel worden gekozen.
Voor- en nadelen van draadvormen

Voordelen:
- Geen spaanvorming, geen spaanafvoer
- Zeer betrouwbaar
- Hoge draadsterkte door koude vervorming
- Stabiel gereedschapsontwerp, dus laag risico op breuk
- Zeer goede oppervlaktekwaliteit
- Eén stuk gereedschap voor blinde en doorlopende bewerkingen
- Zeer lange levensduur mogelijk

Nadelen:
- Hoge eisen aan het voorboren
- Gereedschapsbreuk leidt meestal tot uitval
- In sommige branches niet toegestaan
- Toepassingsgebied beperkt door rek bij breuk, treksterkte en schroefdraadspoed
- Hoog koppel met grote schroefdraadafmetingen
Foutpreventie bij het gebruik van draadvormers
Onze GARANT highlight-producten voor draadvormen:
3. Herstellungsverfahren: Gewindefräsen
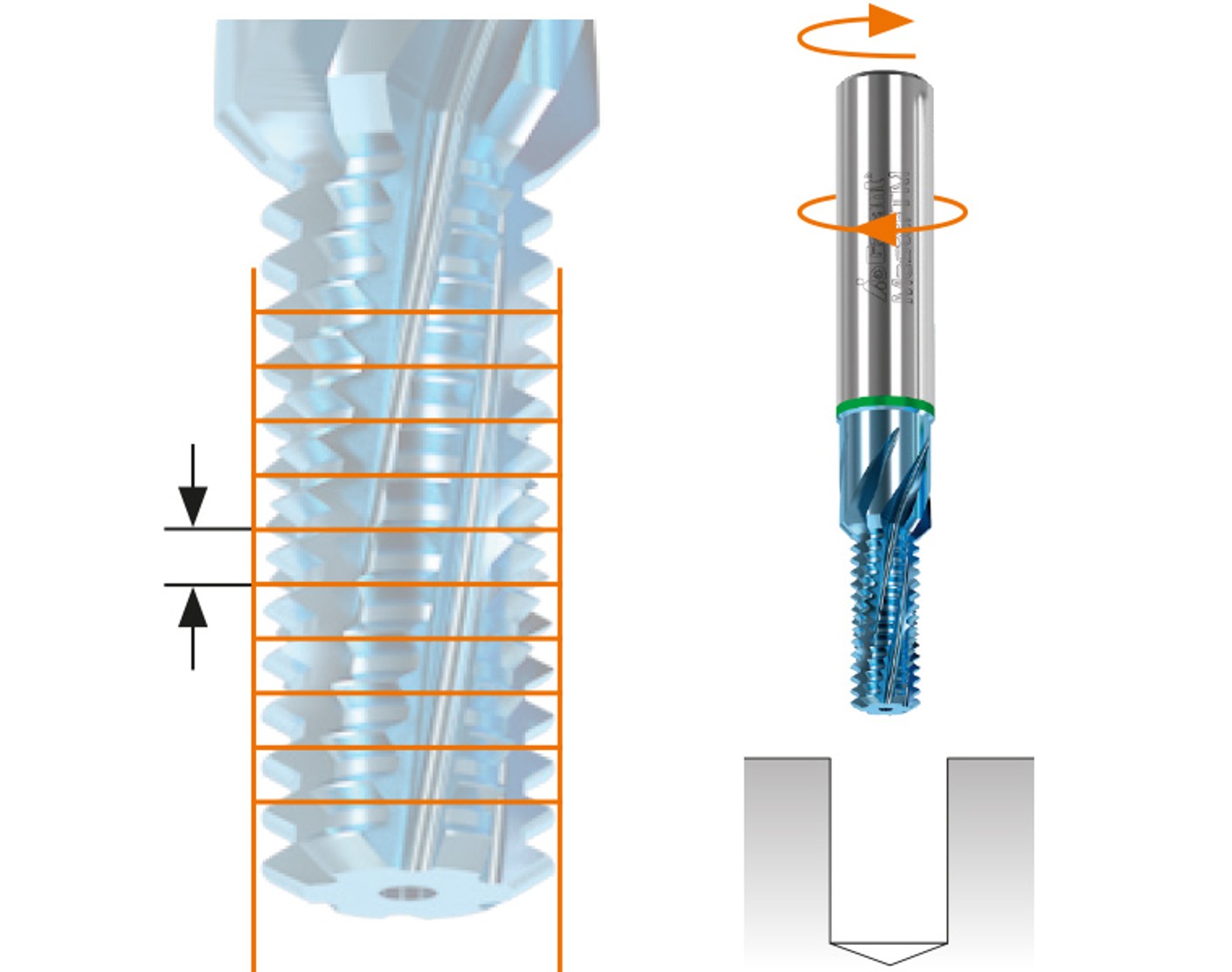
Garenproductie met korte doorlooptijden:
Voorwaarde voor het gebruik van een draadfrees is een 3D-CNC-besturing.
Na het aanzetten tot de werkdiepte, duikt het gereedschap radiaal in het werkstuk in een spiraalbeweging om de belasting te verminderen. De schroefdraad wordt nu in een 360°-beweging geproduceerd door de draadfrees te draaien en gelijktijdig de drie hoofdassen van het bewerkingscentrum te bewegen.
Draadfrezen bieden een breed scala aan mogelijke toepassingen:
- Draadfrezen kunnen universeel worden gebruikt in de meest uiteenlopende materialen.
- Hoge snijsnelheden en voedingen dragen aanzienlijk bij aan tijdsbesparing in de productie.
- Er is geen risico op axiaal verkeerd snijden van de schroefdraad.
- Korte freespanen zijn ook voordelig voor de proceszekerheid.
Voor- en nadelen van draadfrezen

Voordelen:
- Zeer universeel en flexibel in gebruik
- Eén stuk gereedschap voor blinde en doorlopende bewerkingen
- Eén stuk gereedschap voor rechtse en linkse schroefdraad
- Verschillende tolerantieposities mogelijk met één stuk gereedschap
- Procesbetrouwbaarheid dankzij korte spanen, geen spanenwinders
- Gereedschapsbreuk leidt niet tot afwijzing van componenten
- Laag koppel, zelfs bij grote schroefdraadafmetingen

Nadelen:
- Hoge gereedschapskosten
- Complexe programmering en
- eisen aan de machine
- Verwerkingstijd voor massaproductie vaak onrendabel
Managementstrategieën in de tekening
Optimaliseren van het gebruik van de tekening
Bij een draadfrees wordt normaal gesproken de volledige schroefdraad geproduceerd in een 360°-beweging. Voor speciaal ijzer kan een snijkrachtverdeling handig zijn. Ook de verandering van de lusrichting kan het werkresultaat optimaliseren.
Deel programmering:
- Werkmachines werken meestal met hun eigen regelcycli bij het frezen van schroefdraad
- Bij het programmeren van de snijparameters moet erop worden gelet of contourvoeding v of middenbaanvoeding V m moet worden opgegeven
Tip: Maak een proefrit over het werkstuk en let op de cyclustijd
Snijkrachtverdeling (aanbevelingen) voor kritische freesopties:
- Voor draaddiepten >2×D en grote draadspoed (P>1,5 mm), werk met een radiale snijverdeling van 2/3 – 1/3
- Voor dunwandige materialen en onstabiele omstandigheden
- Voor problemen met conische schroefdraadvorming door doorbuiging van het gereedschap
- Torsiekrachten en buigmomenten worden aanzienlijk verminderd door de radiale verdeling van de sneden
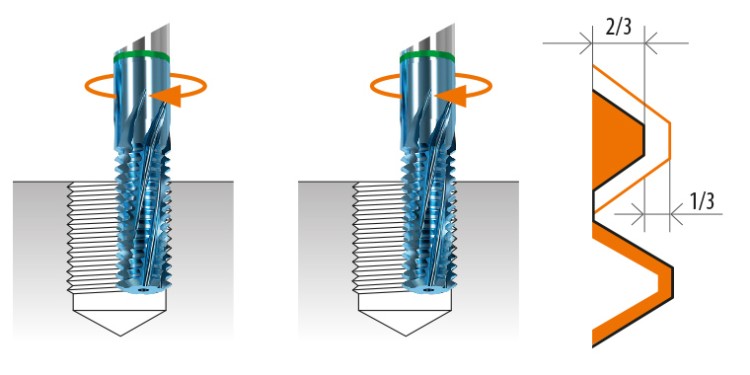
Radiale snijverdeling
Ongeveer 2/3 van de draad wordt eerst gevormd en vervolgens definitief gevormd in een tweede stap.

Axiale snijverdeling
Hier wordt eerst een deel van de schroefdraad geproduceerd en vervolgens wordt de gehele schroefdraaddiepte bewerkt.
De ideale gereedschapsbeweging kiezen:
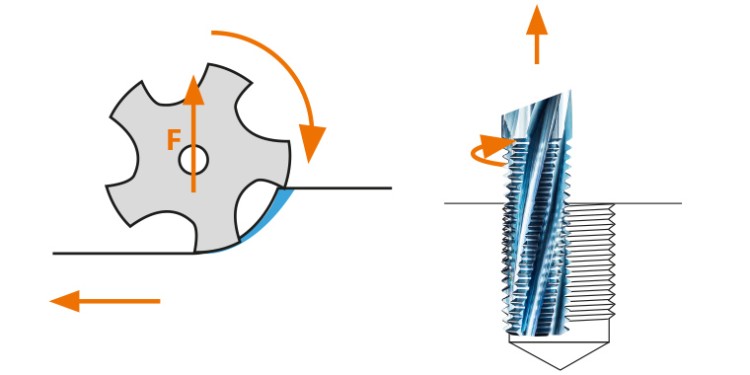
Meelopend frezen
Radiale kracht F werkt in de richting van het middelpunt. Lage spaandikte bij het uittreden van de snijkant.

Gegenlauffräsen
Radial-Kraft F wirkt in Richtung Werkstück. Höhere Spandicke bei Schneidenaustritt

Voordelen:
- Trillingen worden verminderd (klappertekens)
- Verbeterde standtijd
- Door lage snijdruk voor dunwandige werkstukken

Nadelen:
- Hoge gereedschapskosten
- Complexe programmering eneisen aan de machine
- Verwerkingstijd voor massaproductie vaak onrendabel
Boor cirkeldraadfrees:
Bij het cirkelvormig schroefdraadfrezen moet rekening worden gehouden met bepaalde afwijkingen in de bewerkingsstrategie, die verschillen van standaard schroefdraadfrezen.
Snijkrachtverdeling:
Met een cirkelboordraadfrees wordt de schroefdraad in één bewerkingscyclus exact op de schroefdraaddiepte nabewerkt. Een verdeling van de snijkrachten is niet nodig, omdat de optredende radiale krachten constant blijven, zelfs bij verschillende schroefdraaddieptes.
Gereedschap instellen:
Met behulp van de gespecificeerde programmeerradius (RPRG-waarde), die op de schacht is gelaserd, kan de gebruiker met de eerste schroefdraad direct een maatgetrouw tapgat maken.
Strategie:
De boorcirkeldraadfrees is linkssnijdend. Om deze reden wordt rechtse schroefdraad in dezelfde richting bewerkt en linkse schroefdraad in tegenstroom. Koeling met perslucht zorgt voor een maximale standtijd in geharde materialen tot 63 HRC. De schroefdraadbeschermingsverzinkboor kan voor of achteraf worden gemaakt.
Draad freesproces:
De geometrie van de kopsnijkant bepaalt de kerndiameter van de schroefdraad. De kopsnijkant is zo ontworpen dat bij het bereiken van het schroefdraadtolerantiecentrum de kerngat-⌀ binnen de kerngattolerantie ligt. Dit zorgt ervoor dat het kerngat en de schroefdraad nauwkeurig zijn. De eerste snijkant van de cirkelvormige boordraadfrees dient als voorsnijder voor het schroefdraadprofiel. In het draadfreesproces voert het de belangrijkste bewerkingen uit op het voltooide schroefdraadprofiel. De tweede snijkant doet de afwerking. Het bewerkingswerk van de derde snijkant is zeer gering en wordt meer gebruikt voor het reinigen van de schroefdraad dan voor blanco sneden.
Voorkom problemen bij het gebruik van draadfrezen
Onze GARANT highlight-producten voor draadfrezen en rondboren schroefdraadfrezen:
4. Fabricageproces: boren met cirkelvormige draadfrezen

Het fabricageproces van het cirkelvormig boren van draadfrezen:
Net als bij de draadfrees is de voorwaarde voor het gebruik van een cirkelboordraadfrees een 3D-CNC-besturing. In tegenstelling tot draadfrezen, duikt de cirkelboordraadfrees met een spiraalvormige beweging zonder kerngat in het materiaal. Boren, draadfrezen en afschuinen is mogelijk in slechts één bewerking.
Ronddraadfrees als probleemoplosser voor de meest uiteenlopende eisen:
Een cirkelboordraadfrees staat voor proceszekerheid, vooral bij eindbewerkingen op complexe componenten. Het is uitstekend geschikt voor het tappen van schroefdraad op schuine of oneffen oppervlakken.
Afwijken van de cirkelboordraadfrees door schuine schroefdraadin- en uitgangen is niet mogelijk. Het is ook geschikt voor onstabiele klemomstandigheden. Zelfs bij moeilijk te bewerken materialen tot 63 HRC biedt dit gereedschap een uitstekende procesbetrouwbaarheid.