Autonomous production with ongoing process monitoring
Hands off – the premier league
The integration of further solutions for breakage monitoring or recording of measurements or our software solution “Connected Manufacturing”, for example, make completely autonomous production possible. There is no longer a person on site, even readjustment and documentation is done completely automatically, meaning your production will be up to 80% faster.
Intelligent control of machine tools
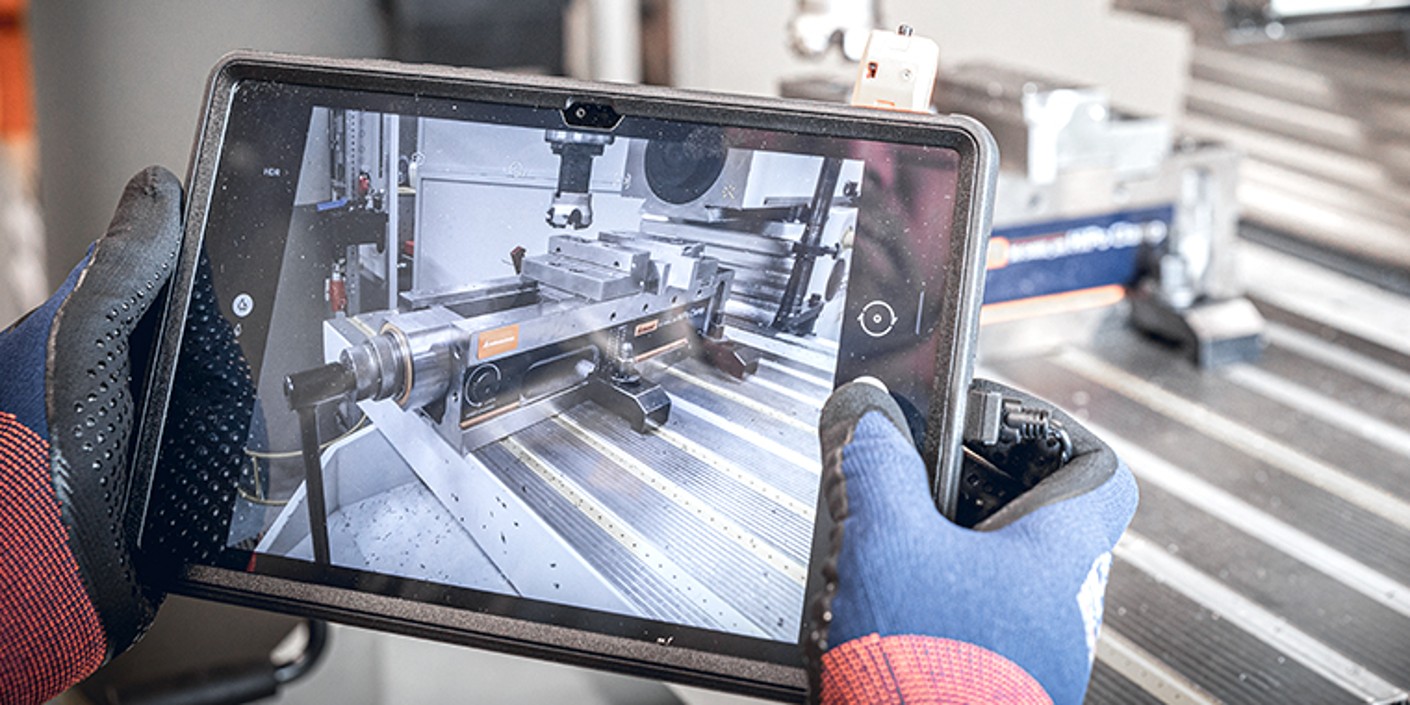
In order to operate an automated production process profitably and reliably, more than just unattended loading and unloading of the machine tool is required. An adapted machining and clamping strategy as well as permanent process control are crucial to industrial automation and serve to sustainably optimise machine processes.
The 7 challenges of automated production
- Position or correct clamping of the component
- Tool wear
- Tool breakage monitoring
- Dimensional accuracy of the component
- Ejection of reject parts
- Stopping the process
- Thermal growth during machining
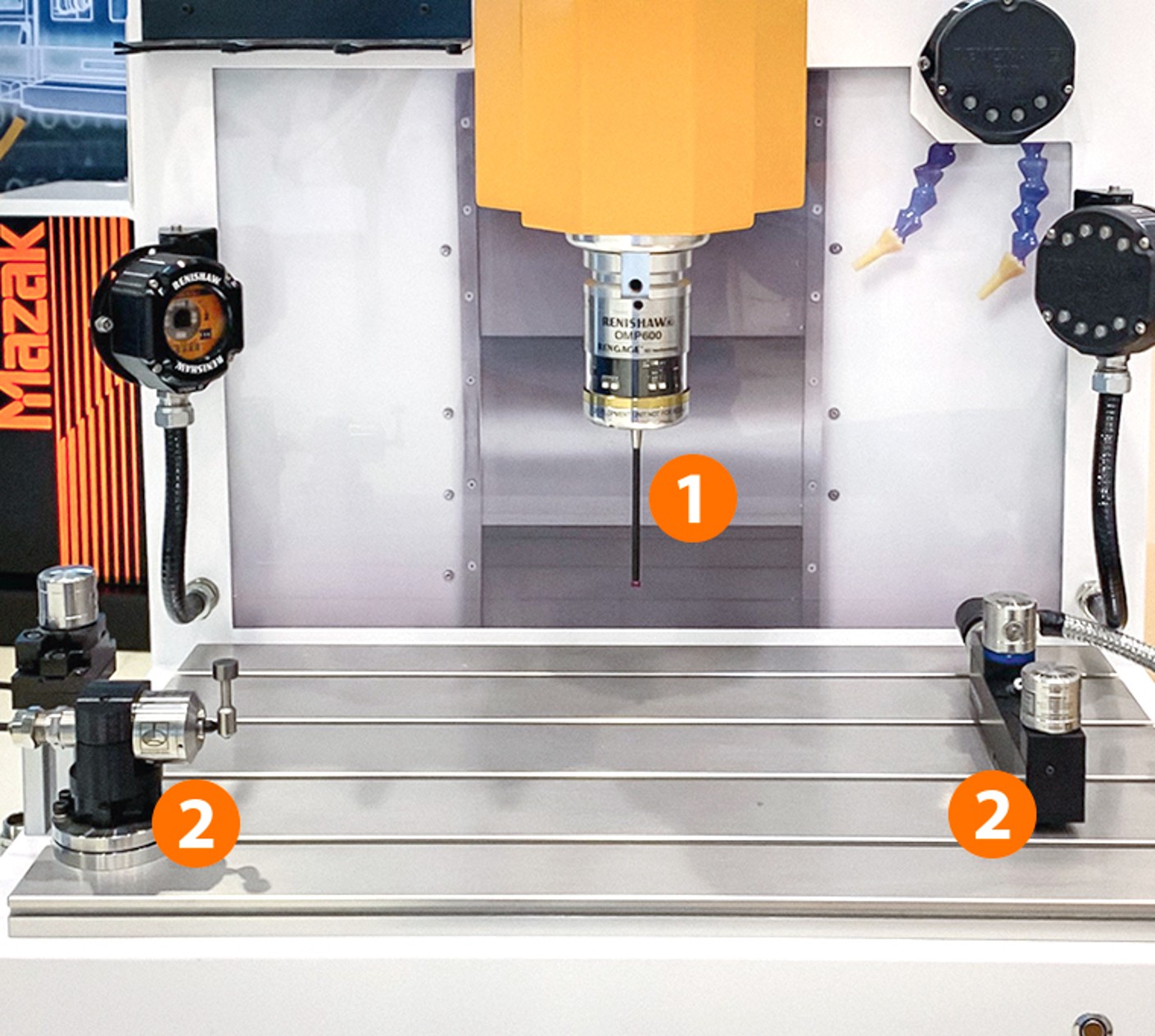
Increasing the degree of automation through measurement technology offers a solution
1) Spindle probe
Probes ensure precise and repeatable measurement of the workpiece and provide data for the next steps:
- Workpiece zero point, position of the component
- Measurement of manufactured features
- Automatic correction of deviations in the event of tool wear
2) Tool setter
The tool setters or tool measuring systems check the tools for breakage or measure their length and size:
- Measurement of the tools (length and radius)
- Tool wear control (length and radius)
- Tool breakage monitoring
Industrial measurement technology: more than component alignment
By using industrial measurement technology in production, you can automate activities that previously had to be carried out manually.
Get advice and sustainably increase the efficiency, quality, capability and accuracy of your machine tools. We advise you with our partner Renishaw. No other company for industrial measurement technology offers this range of technologies to support a fully automated CNC manufacturing process.
The benefits to you:
- Consultation on site during project planning
- Coordinated overall concept, depending on your needs and production environments
- Permanent test documentation for sustainable optimisation of your production processes
We advise you in collaboration with Renishaw regarding:
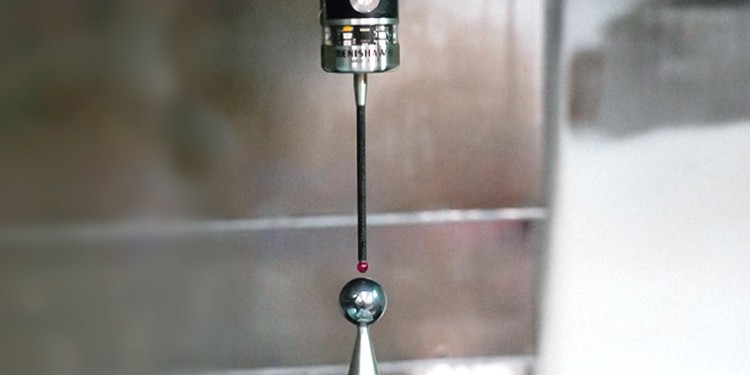
Machine setting
The machine setting determines the alignment and position and enables a machine-specific calculation of the zero-point offset, which reduces deviations between the machines.
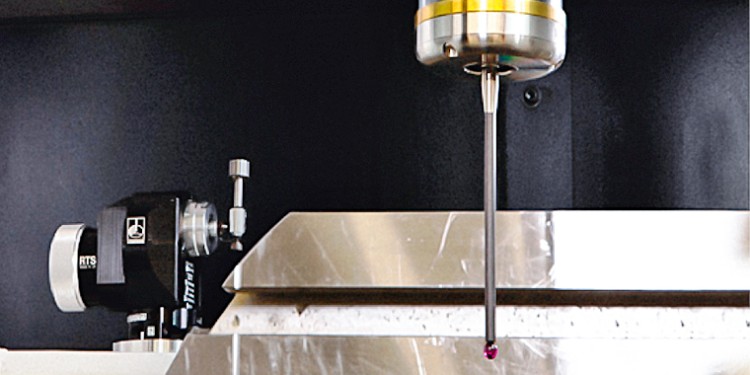
Setting up the tools
Contact and non-contact tool control systems enable unattended operation of machine tools. The tool setting determines the length, radius and/or diameter of the cutting tools and even the state of the cutting edge for automatic calculation and correction of the tool offset.
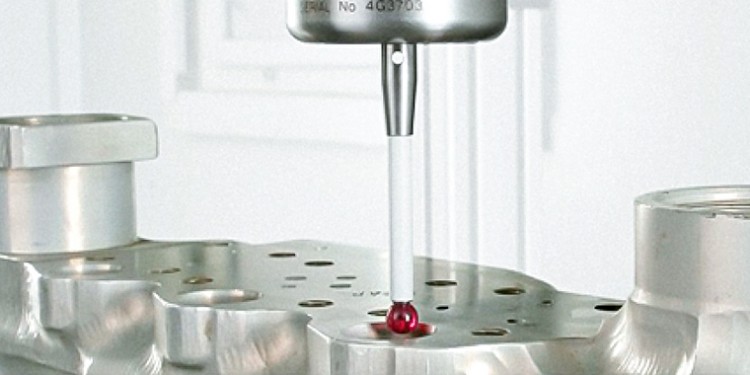
Setting up the workpiece
Traditionally, this would require operator intervention. Now you can use the automatic setup of workpieces in your production environment to define the position of reference features, orientation, size and identification for workpieces.

Tool breakage detection
Automatic tool breakage detection enables unattended operation of machine tools, which means that one operator can easily handle multiple machines. Tool condition monitoring can detect the presence of a tool, the tool position, and broken or knocked edges of the tool.
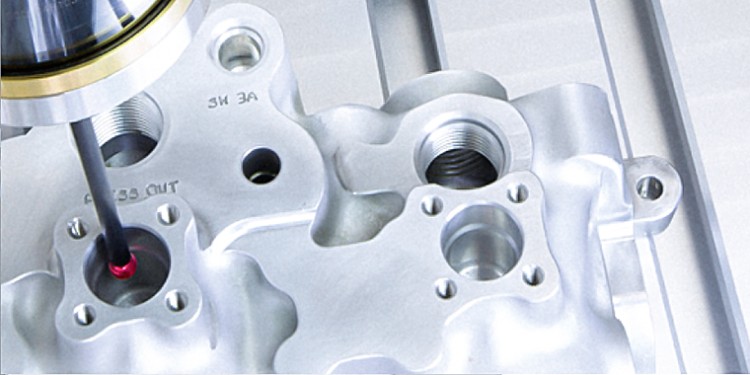
Measurement inside the machine
The measurement in the machining process allows you to adapt the machining to fluctuations in the machining process, workpiece deformation, tool deflection and thermal effects. It enables automatic updating of coordinate systems, parameters and correction values based on actual real-time conditions.
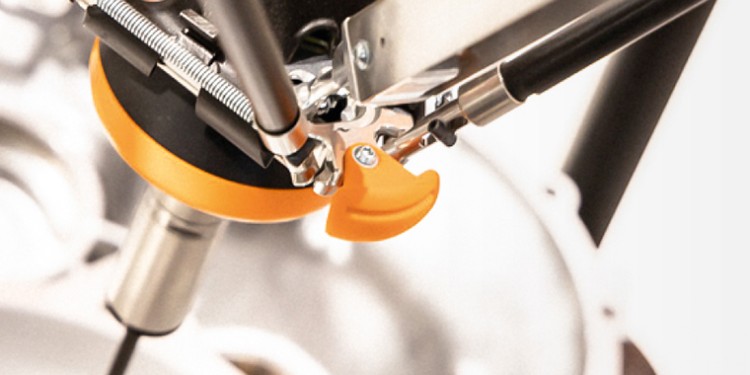
Measurement outside the machine
The introduction of flexible measuring methods in close proximity to production gives you the opportunity to evaluate individual machining processes for automatic process control and thus ensure reliable quality of the manufactured parts.
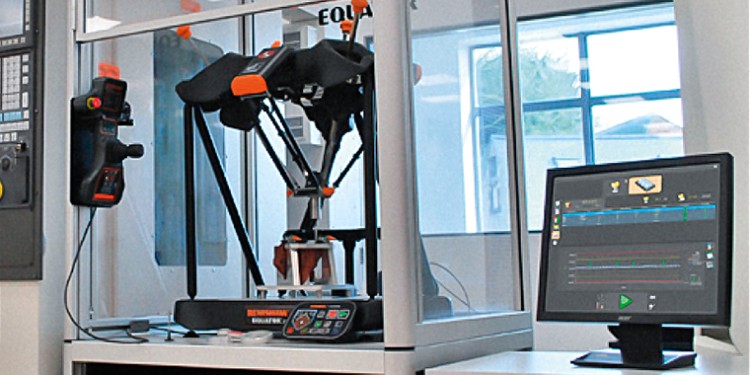
Tracking and monitoring
In addition to tool setting, workpiece detection and tool breakage monitoring, Renishaw technologies can also compensate for changes and process drift caused by tool wear and thermal effects.
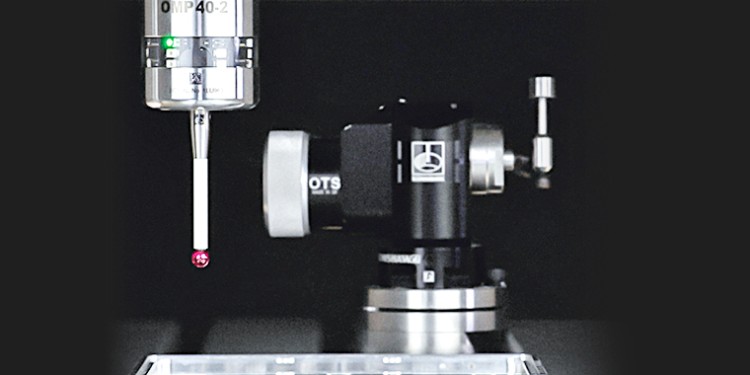
Adjustment of the tools
Automatic resetting of the machining process after a tool change.
Simply full transparency: your production process with Connected Manufacturing
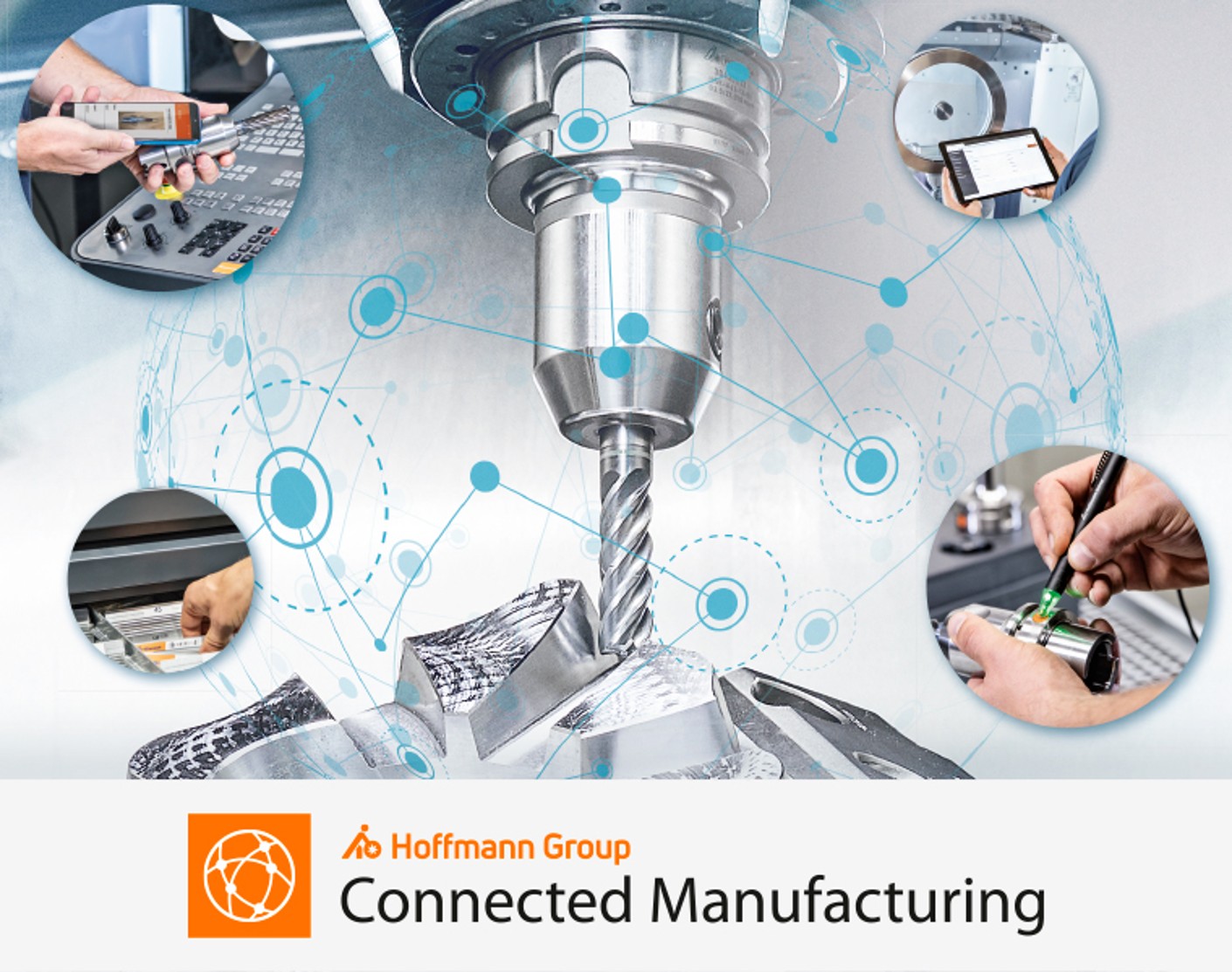
Realise the full potential of your production: with Connected Manufacturing, you can prepare your machine for the next order with repetition accuracy. Setting up outside the machine while processing is still in progress (parallel to the main time) is possible at any time and significantly increases your efficiency. Another key advantage is that all the information about the order and all documents are stored in one central location. So you have everything in view at all times.
The new challenge is unattended production
The use of an automation solution and, above all, completely autonomous production confronts you with important questions:
- How do I know that my machine is still producing and that my components are being manufactured on time?
- How do I design the production process to be as repeatable as possible and the required changeover to be as efficient as possible?
- Where do I find out about the current processing status?
- How do I ensure alternating operations, e.g. with unattended late or night shifts?
Connected Manufacturing offers the solution
With the use of Connected Manufacturing, you have full control at all times.
With Connected Manufacturing, you benefit from features including these:
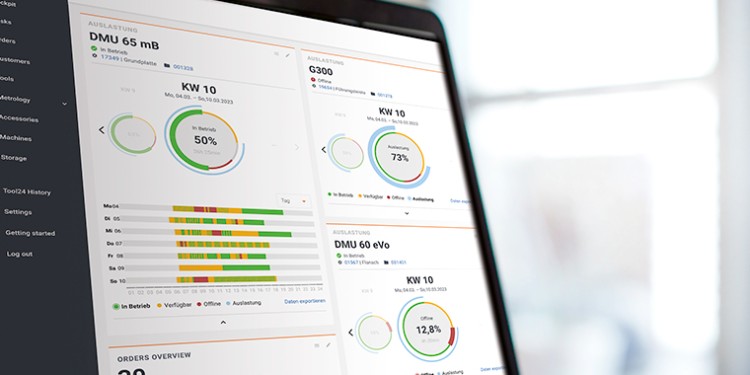
Live status and operational report
Full transparency at all times as to whether your machine is still producing and how efficient production has been in recent days. At a glance full information about:
- Productive time achieved when the machine is switched on
- Operating and spindle times
- Live status of each machine and the current component
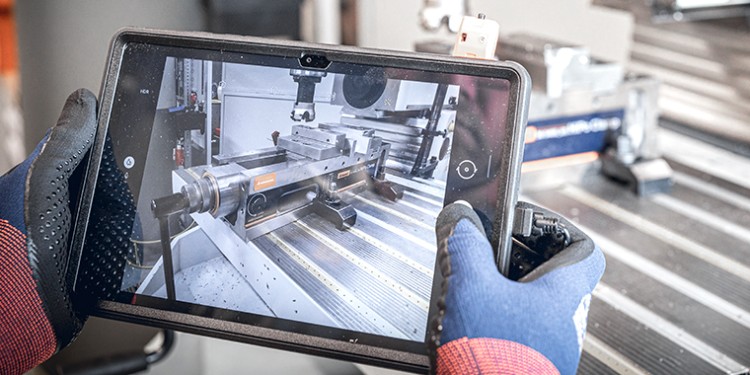
Make knowledge available
Regardless of whether it’s clamping plans, NC files, photos or cutting data, with Connected Manufacturing, you can easily archive and document everything in one central location.
In addition, by connecting to an ERP interface, you can make all your data available throughout the company. This allows, for example, checking of dispatch to be carried out in no time at all.
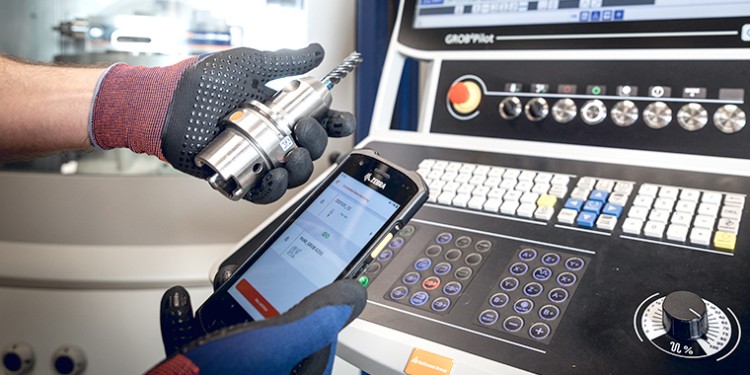
Set up in parallel to the main time
With Connected Manufacturing, you can set up your machine while processing is still in progress. This avoids unnecessary downtime and non-productive times. Tool data and programs are transferred directly – thus avoiding possible sources of error.
A further decisive advantage is that by means of advance set-up, you relieve your tool preparation and increase your quality in tool supply.
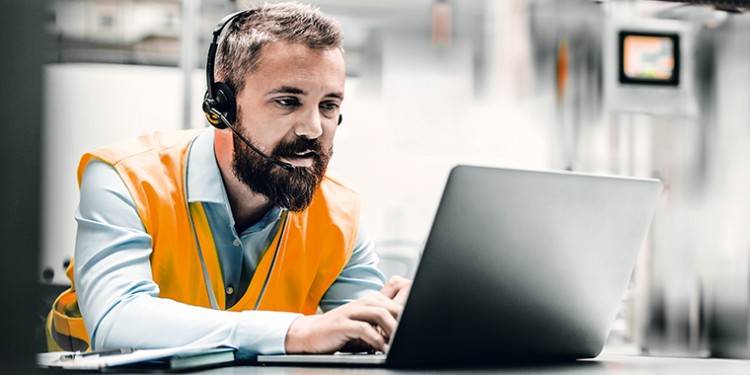
Permanent reporting
Our digital software solution Connected Manufacturing gives you information about the current status of your production order. See today which jobs have to be processed tomorrow, and design your production as efficiently and effectively as possible.
In combination with an ERP interface, the status and runtimes of orders are available throughout your company.