GARANT hydraulic chuck
Extremely slim, innovative and powerful problem solver.
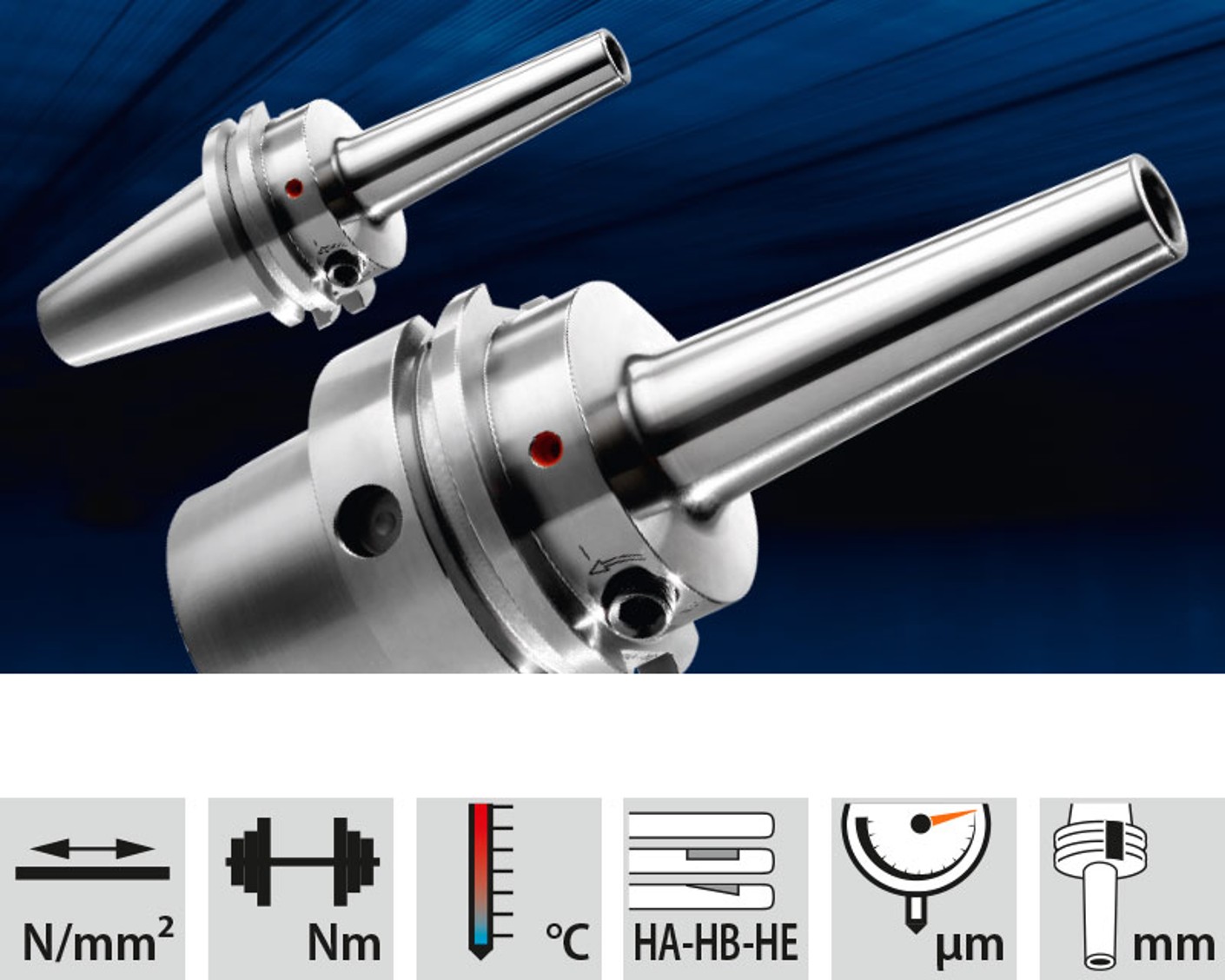
Extremely slim and robust: The GARANT hydraulic chuck, produced using selective laser melting, has many unique advantages and revolutionises clamping technology.
- Thermal stability up to 120 °C
- Maximum process reliability
- Flexibility through the use of reducing sleeves
- Quick, simple tool change
- No risk of accidents through heat (unlike shrink-fit)
- Very good repeatability
- Low setup costs
- Excellent damping characteristics: Reduction of chatter marks, protection of tool cutting edge, protection of machine spindle
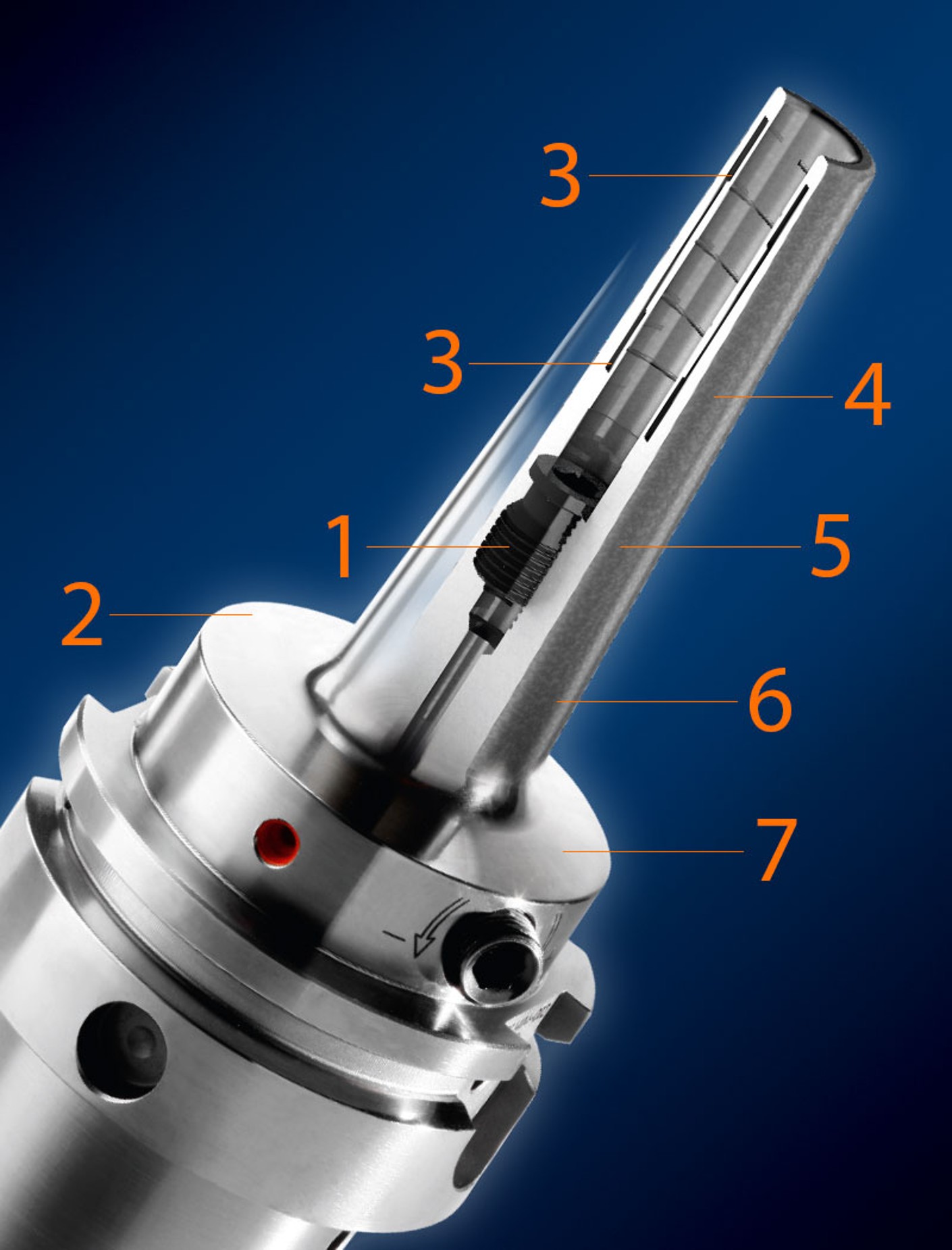
Slim clamping using high-tech
Selective laser melting makes realisation of new, unique geometries possible – which are still powerful, precise and process reliable.
- Able to withstand high stresses: The special metal structure of the new GARANT hydraulic chuck provides similar coefficients of expansion to conventional material.
- Powerful: The new, slim hydraulic chuck displays the same holding torques or clamping forces as a conventional shrink-fit chuck.
- Thermal stability: Due to the sintered construction and enclosed system, soldered pressure chambers are not necessary, making application up to 120 °C possible.
- Universal & reliable: Clamping of tool shanks shape HA, HB and HE.
- High precision: Radial run-out accuracy ≤ 3 µm.
- Extremely slim design: The GARANT hydraulic chuck is of a much slimmer design than conventional hydraulic chucks.
- Low corrosion tendency: Due to special surface treatment.
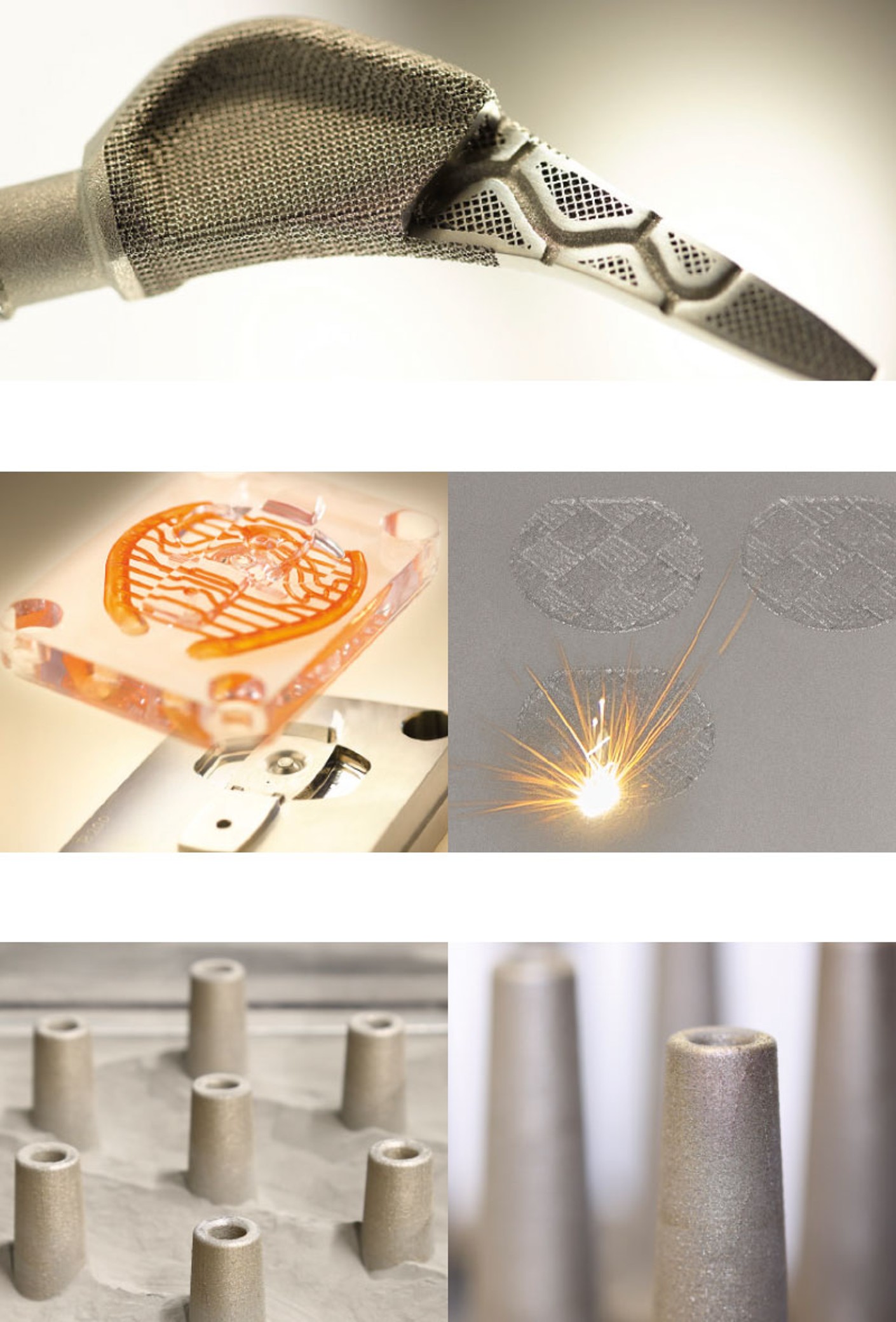
Precision achieved by laser melting
Metal powder melted at more than 1600 °C makes it possible to produce previously impossible geometries.
Exceptional innovations like the GARANT hydraulic chuck require exceptional production methods – selective laser melting.
Freedom of geometry
Realisation of component geometries that would not be possible using conventional machining. Ideal for demanding areas such as medical, aerospace or tool- and mould-making. The GARANT hydraulic chuck can thus be produced with an enclosed pressure system instead of a soldered pressure chamber.
Weight reduction
Using cavities and honeycomb shapes it is possible to produce large components that are of a lower weight but maintain identical stability.
Efficiency and environmental awareness
Almost wastefree production. No machining residues. No coolant.
The GARANT hydraulic chuck
HSK or taper shanks are produced conventionally. Layers of metal powder are applied to the HD (hydraulic) tool bodies by selective laser melting. Subsequent grinding operations are used to finish the chuck.
Products and further information
All slim GARANT hydraulic chucks (contour with 3° taper) can be found here.