Taking a lean approach to procurement logistics boosts transparency and increases revenue.
The big picture: the origins of lean management
The term “lean production” originated in a study by the Massachusetts Institute of Technology (MIT) called “The Machine That Changed The World: The Story of Lean Production”.
Back then, the scientists analysed all the production systems that were found at Japanese car manufacturers at the time, developed based on the model of the Toyota Production System (TPS). The TPS itself was created in the 1950s as a result of a crisis at the Japanese car manufacturer Toyota, because the markets were expecting an ever wider range of vehicles in small volumes. Therefore, two Toyota engineers combined the advantages of mass production (speed, low unit costs) with those of manual production (flexibility and high quality) and designed a new production concept on this basis – called lean. At last, enormous productivity, high quality standards and the ability to adapt flexibly to meet changing customer requirements were made possible.
The elements of lean production have proved their worth to this day, and are synonymous with an efficient and modern material flow in industrial production.
The relevant terms from lean production are now also firmly anchored in the culture of many companies. We say Muda when we talk about preventing activities that do not add value, Muri when we talk about not overloading/overburdening equipment and operators, and Mura when we talk about preventing unevenness.

Muda
Activities that do not add value but that do consume space, effort/money or time without increasing the value of the product.
Muda distinguishes between seven types of waste:
1. Transportation is fundamentally an ancillary process because workpieces, material and tools must inevitably be transported through the Production department.
2. Inventory in the form of material or intermediate or finished products. It masks problems in production, as it is assumed that its existence is intended to compensate for inadequate delivery reliability, high reject rates, poorly coordinated processes or machine failures.
3. Motion when executing processes, such as unnecessary handling, searching or time spent obtaining material and tools from areas away from the workstation. This is caused by an inefficient workstation design and may result in quality defects or even accidents at work.
4. Periods of time spent waiting, in the sense of empty and idle times in which no value is added.
5. Overproduction because more is produced than a customer wants.
6. Unnecessary processing steps, meaning processes or technology that are unnecessarily complex for producing the final product.
7. Defects, as they may negate the value added to the product so far and require resources for potential reworking that would otherwise not be needed.
Muri
Muri stands for overburdening/overloading people and machines beyond the natural limit. This results in a poor working climate, quality problems and accidents or mechanical overload and machine failures.
Mura
Mura describes the uneven utilisation of people and machines. This is caused by irregular production plans due to fluctuations in sales, varying process times or work tasks, or fluctuating production volumes due to machine downtimes and missing parts.
Please note that Mura is also the cause of Muda and Muri: not enough activities that add value are created (Muda) if machines, employees and material are kept on hand despite low capacity utilisation, while higher-than-average capacity utilisation will lead to overburdening/overloading – Muri.
Especially with Muda and when considering motion when executing processes, and specifically the need to prevent unnecessary handling, searching and time spent obtaining material and tools, it is clear that maverick buying sabotages lean management, meaning it should be avoided without fail.
Why efficiency has to start at the workbench
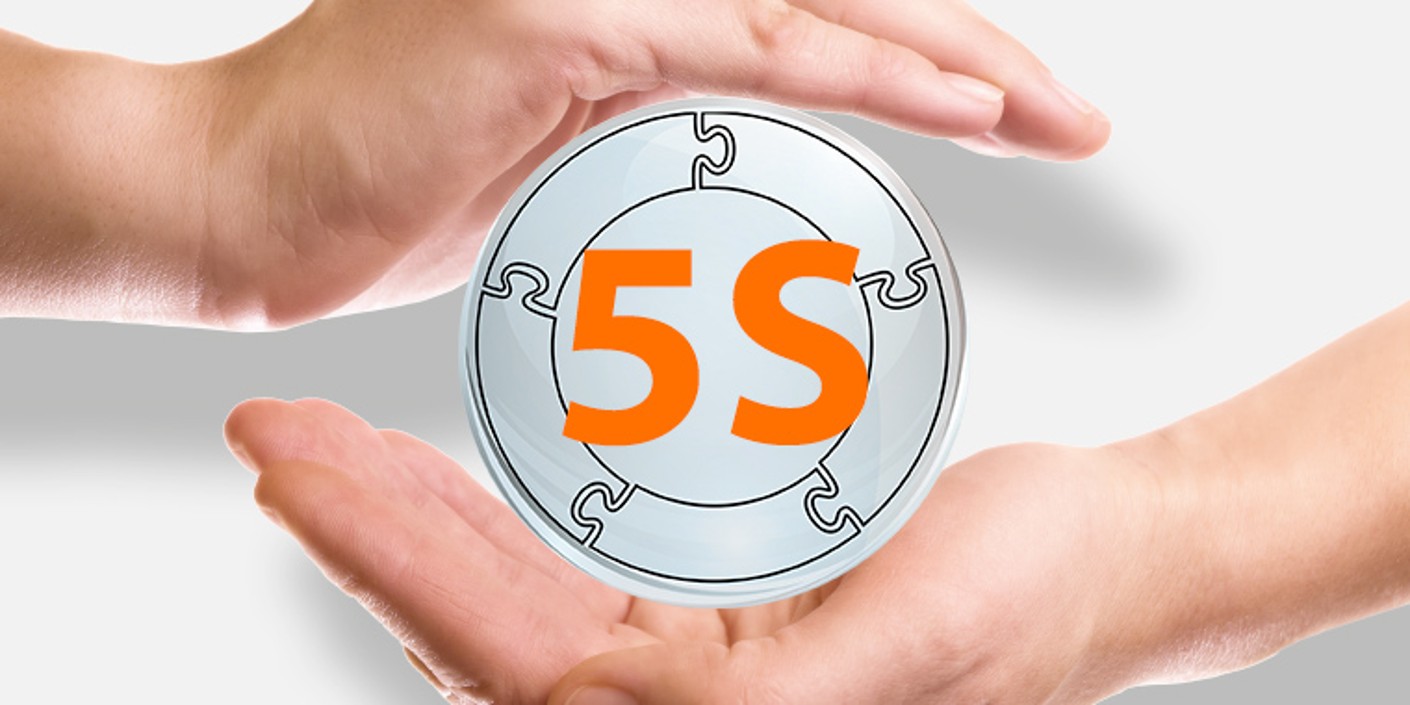
An initial option for overcoming these issues is the so-called 5S methodology, which helps to design workstations in such a way that waste is eliminated. The benefit of this is greater efficiency. In addition, this method provides a clear overview and ensures an orderly workstation, and promotes the use of defined work routines.
This approach guarantees that processes are reproducible, and quality also improves. Employees are less stressed because they do not need to hunt down tools. Your workers are motivated to continue optimising the work environment by themselves, and benefit from the creative potential that is unleashed. Structured, safe and ergonomic workstations also reduce downtimes.
Background: It is no surprise that the 5S methodology also comes from Japan. The idea is to take a systematic approach to designing work environments, so that workers can concentrate on activities that add value while eliminating waste – just like Muda.
How five simple principles will help you add more value:
Motivate your workers to put these principles into practice in their day-to-day working lives. Set a good example in your role as Managing Director, purchasing clerk and master technician.
Have the courage to select only the essentials. Workers who remove anything unnecessary create space for efficiency and creativity. Which tools do we have duplicates of? Which ones are unusable or already heavily worn? Also check the workbench for things that should not be there, such as magazines.
Sort everything in your work area and create a basic level of order. Dispense with equipment that you use only rarely. It is worth considering how to arrange things on the workbench: what do you need all the time, hourly, daily or only weekly or even monthly? Assign each item a fixed place so that it can be found at all times and by anyone.
Keep things clean. In many cases, this alone is half the battle. Determine the necessary cleaning cycles and record them. Maintaining a clean and tidy workbench brings many benefits: any defects identified on tools are immediately rectified by cleaning or replacing them, and you leave a positive impression during customer visits.
Standardise things. Record the results of the 5S methodology and use them to create standards that can be used by all technical disciplines. Regular audits and action plans will make it easier for you to introduce and establish these standards.
Motivate your staff to stay disciplined and to regularly check whether the standards are being met by all workers. To do this, define cycles and set out the arrangements for the monitoring. This will enable you to gradually improve the production workstations on a company-wide basis.