Rationaliser la logistique d'approvisionnement : plus de transparence pour gagner plus.
Les origines du Lean Management
Le concept de "Lean Production" trouve son origine dans une étude du Massachusetts Institute of Technology (MIT) intitulée "The Machine That Changed The World: The Story of Lean Production" (La machine qui a changé le monde : histoire de la Lean Production).
Dans cet ouvrage, les scientifiques ont analysé tous les systèmes de production utilisés par les constructeurs automobiles japonais, qui ont été développés sur le modèle du Toyota Production System (TPS). Le TPS est apparu au cours des années 1950, à la suite d'une crise chez le constructeur automobile japonais Toyota, dans un contexte où les marchés attendaient une gamme de véhicules toujours plus large, produite en petites séries. A l'époque, deux ingénieurs de Toyota ont cherché à associer les avantages de la production de masse (rapidité, faibles coûts unitaires) et ceux de la production artisanale (flexibilité et haute qualité) en élaborant un nouveau concept de production : Lean. Il était désormais possible de concilier énorme productivité, normes de qualité élevées et adaptation flexible aux demandes variables des clients.
Les principes de "Lean Production" ont depuis largement fait leurs preuves et sont synonymes de flux de matériel efficace et moderne dans la production industrielle.
Aujourd'hui, le vocabulaire de la "Lean Production" est solidement ancré dans la culture de nombreuses entreprises. Ainsi, Muda désigne l'élimination des activités non créatrices de valeur ajoutée, Muri, la suppression des surcharges et Mura, celle des déséquilibres.

Muda
Activités non créatrices de valeur ajoutée qui consomment de l'espace, de l'argent ou du temps, sans augmenter la valeur du produit.
Le muda distingue sept types de gaspillages :
1. Les transports sont essentiellement des processus de soutien, car des pièces, matériaux ou outils doivent forcément être transportés tout au long de la production.
2. Stocks de matériaux, produits intermédiaires et produits finis. Ces stocks dissimulent des problèmes dans la production, car l'on part du principe que leur présence est censée compenser un non-respect des délais de livraison, des taux de rebut élevés, des processus mal coordonnés ou des pannes de machines.
3. Déplacements ou mouvements lors de l'exécution du processus, tels que les manipulations inutiles, les opérations de recherche ou de récupération de matériaux et d'outils à distance du poste de travail. Cause : un agencement inefficace du poste de travail. Conséquences : défauts de qualité, voire accidents du travail.
4. Périodes d'inactivité et d'attente sans création de valeur.
5. Surproduction (la production est supérieure à la demande du client).
6. Les étapes de traitement inutiles désignent des processus ou des technologies inutilement complexes pour la fabrication du produit final.
7. Erreurs, car elles peuvent parfois ignorer la valeur ajoutée déjà apportée au produit et génèrent l'utilisation inutile de ressources pour d'éventuelles reprises/retouches.
Muri
Le muri est une surcharge des personnes et des machines au-delà de la limite de charge naturelle. Conséquences : mauvaise ambiance de travail, problèmes de qualité, accidents, surcharges mécaniques et pannes de machines.
Mura
Le mura décrit la charge de travail inégale des personnes et des machines. Causes : plans de production irréguliers en raison des fluctuations des ventes, temps de processus ou contenus de travail inégaux, ou encore volumes de production variables en raison d'arrêts de machines et de pièces manquantes.
Attention: le mura est en même temps la cause du muda et du muri : il n'y a pas suffisamment d'activités créatrices de valeur (muda) lorsque l'on conserve des machines, des personnes et du matériel sous-utilisés. Une utilisation excessive entraîne une surcharge (muri).
En ce qui concerne le muda et l'aspect déplacements/mouvements lors de l'exécution du processus sous l'argument manipulations inutiles, opérations de recherche ou récupération de matériaux et d'outils, il apparaît que "l'achat Maverick" mine le "Lean management" et doit être impérativement évité.
Pourquoi l'efficacité doit commencer au niveau du poste de travail
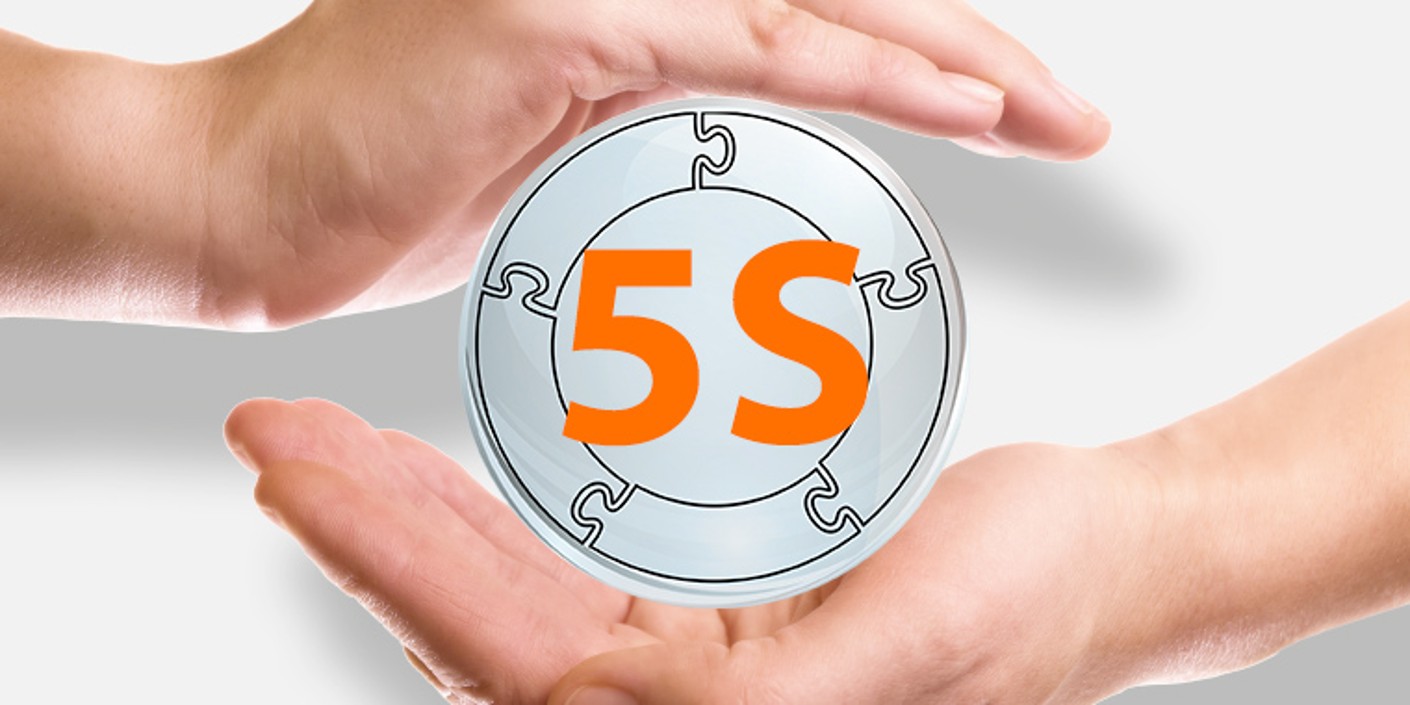
Une première possibilité dans cette optique est la méthode des 5S, qui permet de configurer les postes de travail pour éviter le gaspillage. Effet positif : une plus grande efficacité. Cette méthode permet également de créer un poste de travail plus clair et plus ordonné et favorise les routines de travail.
La reproductibilité des processus est assurée. Dans le même temps, la qualité s'en trouve augmentée. Les collaborateurs sont moins stressés car ils n'ont pas à rechercher/trouver les outils. Ils sont motivés pour continuer d'optimiser spontanément l'environnement de travail et peuvent libérer leur potentiel créatif. En outre, des postes de travail structurés, sûrs et ergonomiques permettent de diminuer les temps d'arrêt.
Contexte : on ne sera pas étonné d‘apprendre que la méthode des 5S provient également du Japon. L'idée : agencer l'environnement de travail de manière systématique pour que les travailleurs puissent se concentrer sur les activités à valeur ajoutée tout en évitant les gaspillages. Comme le décrit le muda.
Comment cinq principes simples permettent de créer davantage de valeur :
Incitez vos collaborateurs à appliquer ces principes. Et donnez l'exemple en tant que dirigeant, acheteur ou contremaître.
Osez faire le tri. Les travailleurs qui éliminent le superflu libèrent de l'espace pour l'efficience et la créativité. Quels outils sont en double ? Lesquels sont inutilisables ou déjà très usés ? Recherchez sur les postes de travail des objets qui n'ont rien à y faire (des magazines, par exemple).
Faites le tri dans votre espace de travail et établissez un ordre de base. Séparez-vous des outils rarement utilisés. Il est judicieux de réfléchir à l'agencement du poste de travail : de quoi avez-vous besoin en permanence, chaque heure, tous les jours, ou seulement une fois par semaine ou même tous les mois ? Attribuez à chaque objet une place fixe. Pour que chacun sache toujours où le trouver.
Veillez à assurer la propreté sur le lieu de travail. En y parvenant, vous aurez déjà accompli la moitié du chemin. Définissez des cycles de nettoyage et documentez-les. La propreté sur le poste de travail est profitable en ce qu'elle permet d'éliminer immédiatement, par nettoyage ou remplacement, les défauts identifiés sur les outils. Sans oublier l'impression positive laissée aux clients en visite.
Etablissez des normes. Documentez les résultats de la méthode des 5S et faites-en des normes qui pourront être appliquées dans tous les secteurs. Des plans d'action et des audits réguliers faciliteront la mise en place de ces normes.
Incitez le personnel à pratiquer l'autodiscipline et à vérifier régulièrement que les normes sont appliquées par tous. Définissez pour cela des cycles et notamment des cycles de passage en vue d'un contrôle. Vous pourrez ainsi améliorer progressivement, à l'échelle de l'entreprise, les postes de travail de production.