ToolGrinding - professional reconditioning of your cutting tools
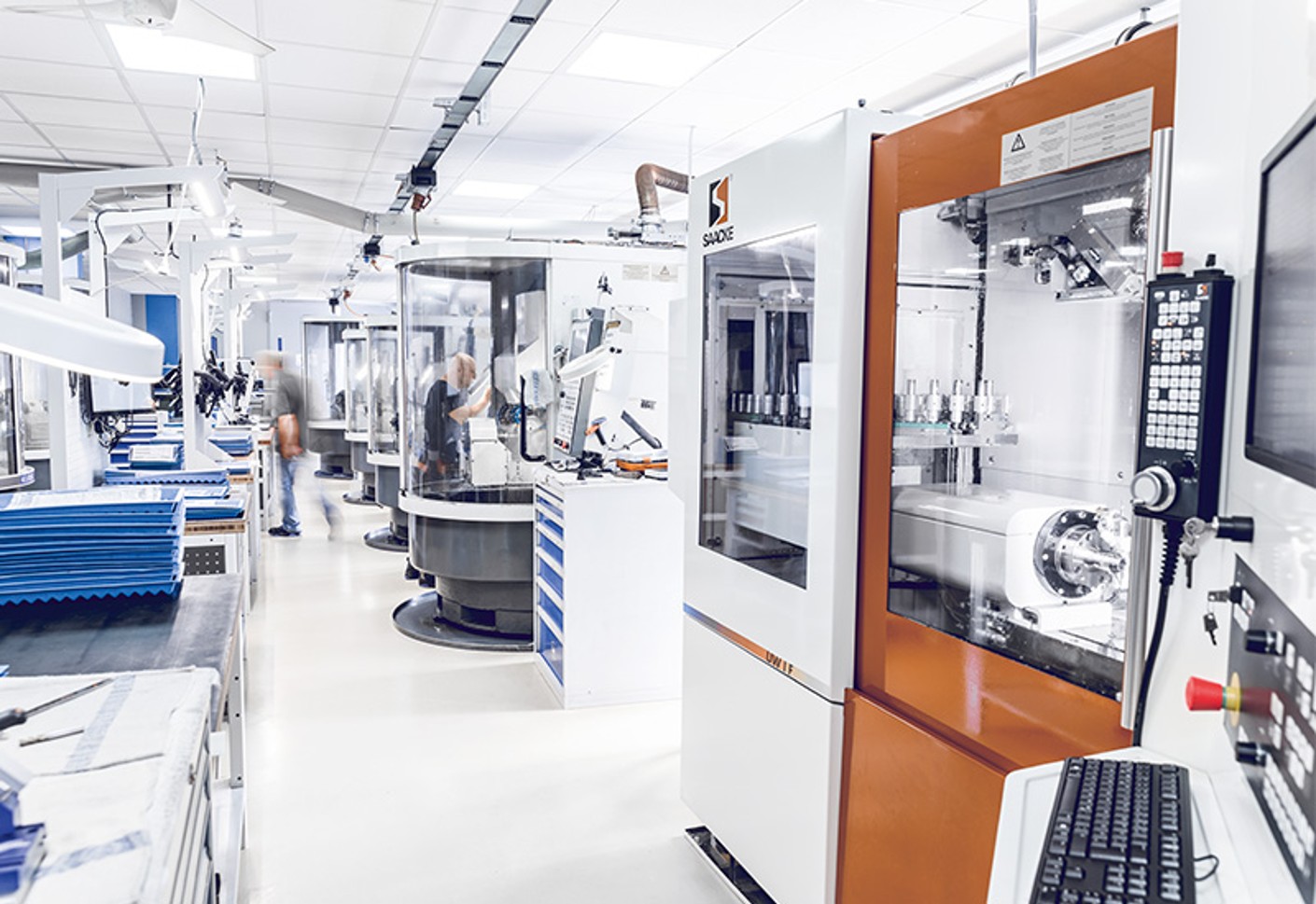
Hoffmann Group regrinding service ToolGrinding
- Bundled manufacturing competence at the Hoffmann Group TechnologyCentre
- Professional team of experts
- Soundly based expert advice
Highest levels of care during checking, reconditioning and return packaging. Prior to grinding, we check your machining tools for type and scope and for cost-effectiveness of the necessary reconditioning. Tools which can no longer be reground of for which regrinding is no longer cost-effective are identified and returned to you free of charge.
We restore your tools back to their original quality. Let us regrind your machining tools. Because nothing is as good as the original.
Your advantages
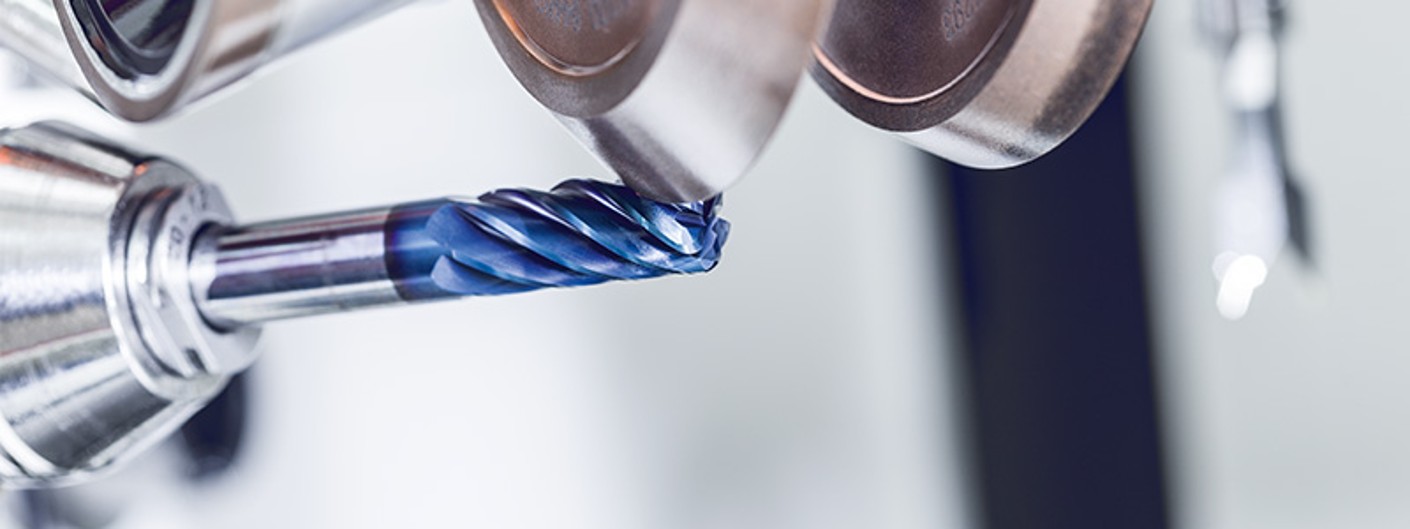
Full performance for your tools
Original manufacturer regrinding, on the machines used for the original production, with the original geometry and the original coating, permits 100% cutting performance at up to 95% tool life - and this applies to every regrind.
Save up to 85% of the cost by choosing an original regrind
The longer you can maintain the original quality of e.g. your drill or milling cutter, the greater your cost saving:
- Reduced storage and capital costs
- Higher availability
- Reduced circulation times at very high productivity and maximum process reliability.
This is exactly what we guarantee, if you trust us with your tools.
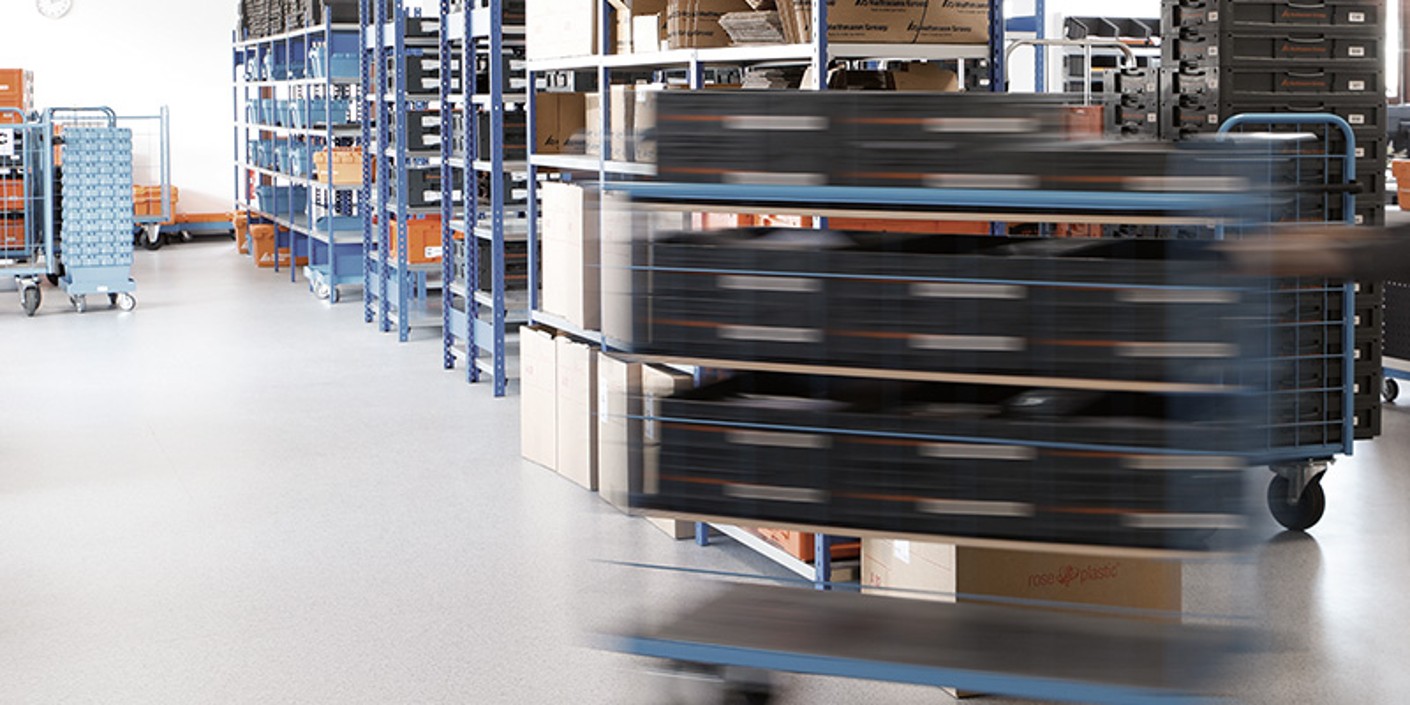
Efficient logistics
- Simple collection and delivery service
- Can also be organised using GARANT Tool24 tool issuing system
- Saves time and trouble
- Sets you free to concentrate on your core competence - machining
Fair transparent prices
Keep track of your costs
- No hidden surcharges
- Fair assessment, no unnecessary loss of cutting edges
- Regrinding only to the extent necessary (depending on the wear and type of tool)
- Prices fixed for 2 years
Semi-standard tools to meet customer requirements
Intermediate sizes for proven types of milling cutter
- Modification of corner radii
- Individual shank recesses (also for new tools)
Services and range of products
The following products are suitable for reconditioning:
- HSS drills
- Solid carbide drills
- Taps & plain shank thread mills
- Countersinks
- Reamers
- Circular saw blades
- Milling cutters
- HSS milling cutters
- Solid carbide milling cutters
- Solid carbide interchangeable head system GARANT TopCut
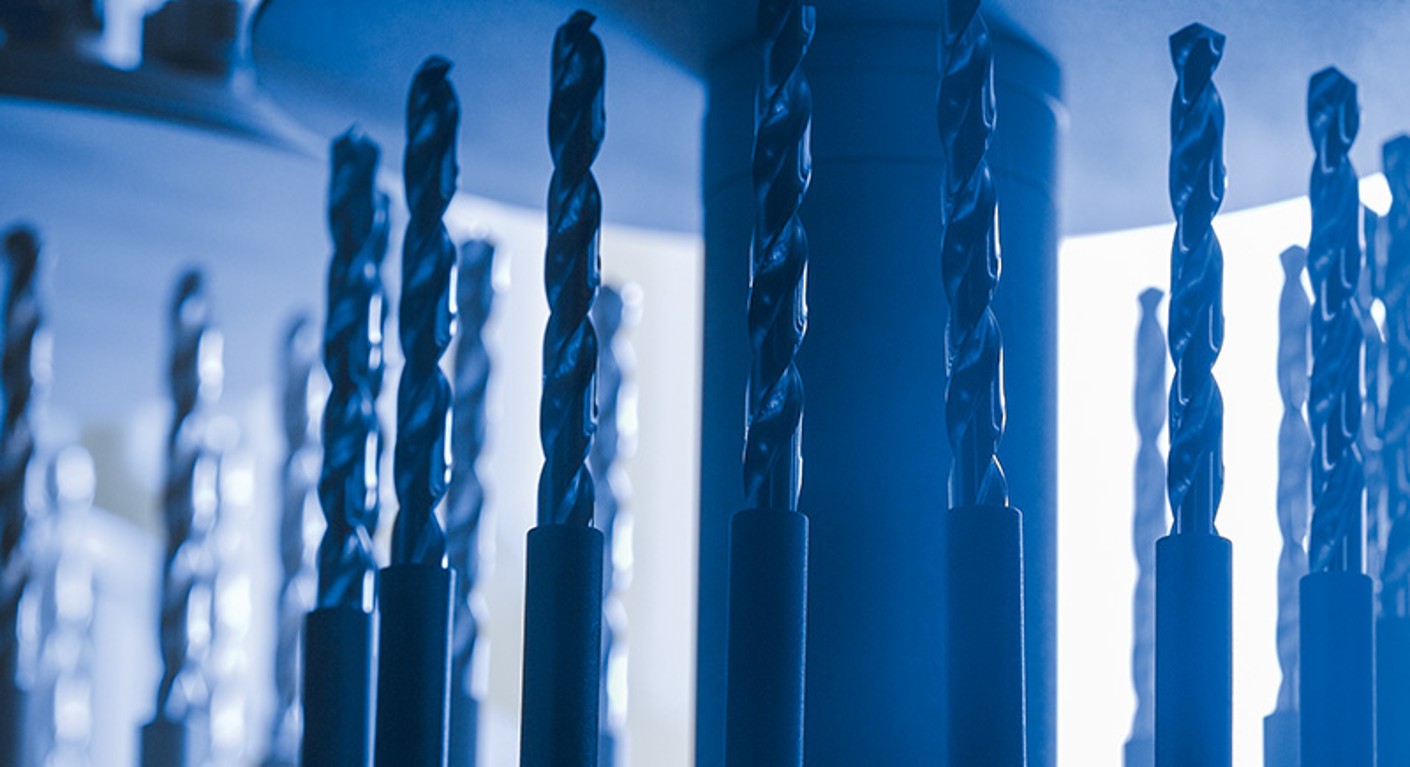
Coating service
- Coating of uncoated new tools, in just a few days; coating to your requirements (subject to compatibility of the desired coating with the machining tool).
- Higher performance because of increases in feeds and speeds.
- Longer tool life.

Measurement report service
If desired you can receive a measurement report, both for new tools and also for resharpened tools. This records the following measurements:
- Radius accuracy
- Cutter diameter accuracy
- Position and shape of steps
- Size and position of chamfers and much more
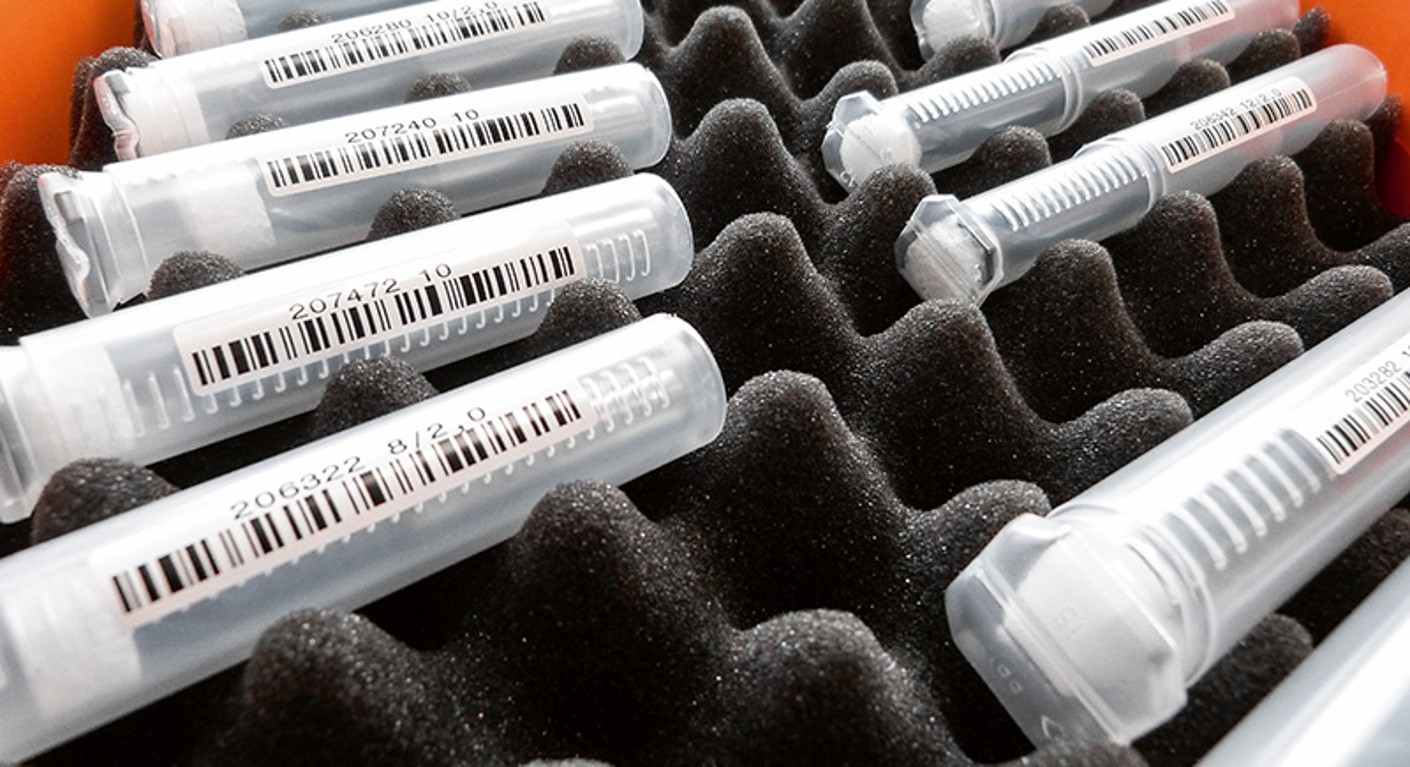
Labelling service
On request we will print the original catalogue number, size and barcode on the reground tool on the outer packaging.
- Quick assignment of your reground tools.
- Ideal for GARANT Tool24 systems.
- Available for all Hoffmann Group catalogue tools.
Service shank grinding retainer function
To use shrink-fit chucks with retainer function No. 302312/2314/7945/7947 the shank of the milling cutter has to have a special clamping flat. This special shank grinding can be ordered under the Hoffmann service number SZ2025, stating the suitable size.
GARANT Master Alu – our specialist tools for drilling in aluminium
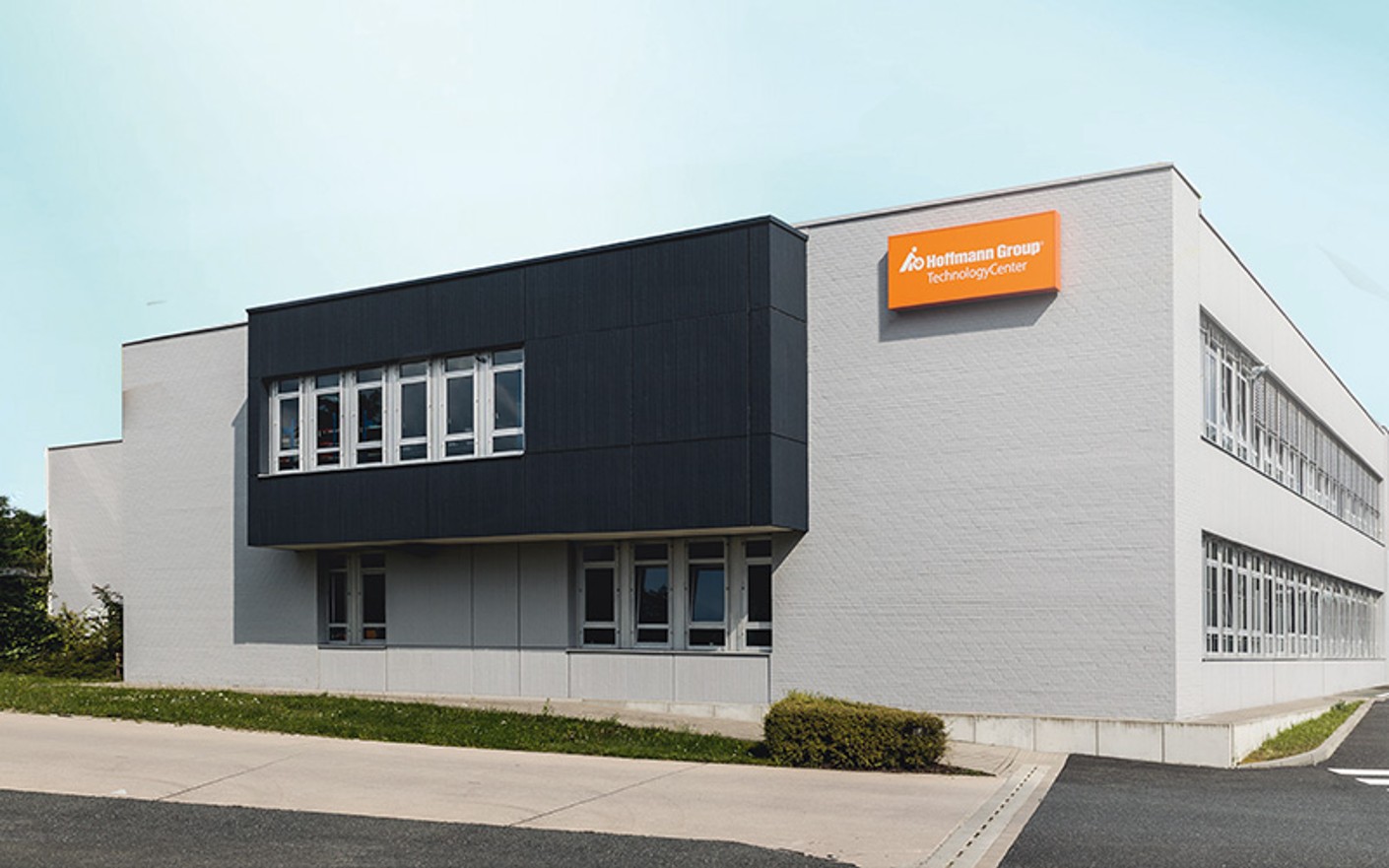
Contact & information
Please contact us if you have any further questions:
Email: Regrinding@hoffmann-group.com
(Hotline Germany)
Hoffmann Supply Chain GmbH
ServiceCenter – Nachschleifservice
Poststraße 15b
D-90471 Nürnberg
Germany