Prozesssichere Gewindeherstellung - Herstellung von Innengewinden
Erfahren Sie alles Wichtige über die verschiedenen Innengewinde-Herstellungsverfahren
In der Fertigungstechnik zählt die Herstellung von Innengewinden zu den anspruchsvollsten Bearbeitungsaufgaben.
Das Gewinde steht oft am Ende eines Herstellungsprozesses und ist damit entscheidend für die Qualität des Werkstückes. Fehlerhafte Gewinde bedeuten meist hohe Mehrkosten. Prozesssicherheit hat absoluten Vorrang, aber auch kurze Taktzeiten und wirtschaftliche Fertigungsabläufe müssen beachtet werden.
Folgende Gewinde-Herstellungsverfahren finden Sie hier auf einen Blick:
1. Herstellungsverfahren: Gewindebohren
2. Herstellungsverfahren: Gewindeformen
3. Herstellungsverfahren: Gewindefräsen
4. Herstellungsverfahren: Bohrzirkulargewindefräsen
Hinführung: Grundbegriffe zum Thema Gewinden
Allgemeine Bezeichnungen und Hinweise:
1. Herstellungsverfahren: Gewindebohren

Das universelle Verfahren für Innengewinde.
Das Gewindebohren ist das bekannteste Verfahren zur Herstellung von Innengewinden.
Hohe Produktivität, vergleichsweise niedrige Kosten und universelle Einsatzmöglichkeiten (auf konventionellen Werkzeugmaschinen, Transferanlagen, BAZ) stehen hier im Vordergrund. Gewindebohrer aus HSS /HSS-E /HSS-E-PM/VHM erfüllen die jeweiligen Anforderungen des Anwenders.
Besonderheiten der Gewindeherstellung
Während der Gewindeherstellung besteht ein Formschluss zwischen Werkzeug und Werkstück. Gewindegröße, Gewindesteigung und Toleranz sind exakt über den Gewindebohrer definiert. Daraus ergeben sich im Vergleich zum Bohren oder Fräsen jedoch spezifische Probleme bei der Bearbeitung:
- Axiale und radiale Bewegungen in Kombination
- Kontrolle des Spindelspieles notwendig, um Steigungsfehler zu vermeiden
- Vorschub und Schnittgeschwindigkeit stehen in direktem Zusammenhang
Die Drehgeschwindigkeit der Maschinenspindel muss mit der Geschwindigkeit der Vorschubachse synchronisiert werden.
Durchgangs- und Grundlochgewinde
Bei der Auswahl des Gewindebohrers sollte eine möglichst lange Anschnittform gewählt werden. Ein langer Anschnitt beansprucht das Werkzeug weniger stark, die Schneidkantenbelastung wird reduziert. Dieser Aspekt gewinnt bei steigender Materialfestigkeit an Bedeutung.
Durchgangsloch-Gewindebohrer
Bei diesen (gerade genuteten) Gewindebohrern mit Schälanschnitt wird der Span in Vorschubrichtung nach unten abgeführt und fällt bei Austritt des Werkzeuges nach unten. Deshalb sind diese Werkzeuge nicht für die Grundlochbearbeitung geeignet. Bei der Drehrichtungsumkehr (reversieren) würde der gestauchte Span nicht abgeschert werden und verklemmen.
Bei einem Einsatz dieser Gewindebohrer zur Grundlochbearbeitung wären Beschädigungen des Gewindes oder Werkzeugbrüche unvermeidlich. Bei der Bearbeitung spröder Materialien kommen gerade genutete Gewindebohrer ohne Schälanschnitt zur Anwendung. Durch die Neigung der spröden Materialien zur Bröckelspanbildung können Werkzeuge dieser Bauweise sowohl zur Durchgangsloch- als auch zur Grundlochbearbeitung eingesetzt werden.

Form A
6 - 8 Gang Anschnitt, für kurze Durchgangslöcher.

Form B
4 - 5 Gang mit Schälanschnitt, universell für Durchgangslöcher

Form D
4 - 5 Gang Anschnitt, für Durchgangs- oder Grundlöcher
Grundloch-Gewindebohrer
Allgemein stellt die Herstellung eines Grundloch-Gewindes höhere Ansprüche an das Werkzeug. Die Späne müssen über die Spannut nach oben befördert werden. Beim Reversieren und Abscheren der Spanwurzel wirken hohe Torsionskräfte auf den Gewindebohrer ein.

Form D
4 - 5 Gang Anschnitt, für Grundlöcher mit langem Gewindelauf.

Form C
2 - 3 Gang Anschnitt, für universellen Einsatzbereich.

Form E
1,5 - 2 Gang Anschnitt, kurzer Gewindeauslauf für größtmögliche Gewindetiefen.
Vor- und Nachteile des Gewindebohrens

Vorteile:
- Breites Einsatzgebiet in fast allen Werkstoffen
- Keine besonderen Anforderungen an die Maschine
- Gewinde können ggf. mit gleichem Werkzeug nachgeschnitten werden
- Handeinsatz ist grundsätzlich möglich
- In der Regel kostengünstige Lösung zur Gewindeherstellung

Nachteile:
- Spanabfuhr sorgt oft für Probleme
- Prozessunsicherheit durch Bildung von Spänewicklern
- Werkzeugbruch führt in der Regel zum Ausschuss
Fehlervermeidung bei der Verwendung von Gewindebohrern
Einteilung in Leistungskategorien
Für die einfache und richtige Produktauswahl sind unsere Gewindebohrer in Gruppen eingeteilt:
Unsere GARANT Highlight Produkte zum Gewindebohren:
2. Herstellungsverfahren: Gewindeformen

Beim Gewindeformen werden die Gewinde durch Kaltverformung erzeugt, Spanbildung und Spanevakuierung entfallen. Durch diesen Vorteil kann der Gewindeformer prozesssicher für Grund- und Durchgangslochgewinde eingesetzt werden, auch bei kritischen L×D Verhältnissen von über 4×D Gewindetiefe.
Belastungsphasen im Gewindeformprozess
Die Drehmomentbelastung auf das Werkzeug liegt beim Gewindeformen bis zu 30% höher im Vergleich zum Gewindebohren. Da ein Gewindeformer keine Spankammern zur Späne Evakuierung benötigt, kann der Seelendurchmesser am Werkzeug stabiler ausgelegt werden. Hierdurch kann ein Gewindeformer auch bei höchsten Anforderungen prozesssicher eingesetzt werden.
Folgende Faktoren haben den größten Einfluss auf die Drehmomententwicklung:
- Werkstückwerkstoff
- Vorbohrdurchmesser
- Gewindesteigung
- Schmierung
- Beschichtung und Geometrie
Um die Drehmomentkräfte möglichst gering zu halten, sollte der optimale Kernlochdurchmesser und ein hochwertiges Schmiermedium gewählt werden
Vor- und Nachteile des Gewindeformens

Vorteile:
- Keine Spanbildung, Spanabfuhr entfällt
- Sehr prozesssicher
- Hohe Gewindefestigkeit durch Kaltverformung
- Stabiles Werkzeugdesign, dadurch geringe Bruchgefahr
- Sehr gute Oberflächengüte
- Ein Werkzeug für Grund- und Durchgangslochbearbeitung
- Sehr hohe Standzeiten möglich

Nachteile:
- Hohe Anforderung an die Vorbohrung
- Werkzeugbruch führt in der Regel zu Ausschuss
- In manchen Branchen nicht zugelassen
- Einsatzgebiet begrenzt durch Bruchdehnung, Zugfestigkeit und Gewindesteigung
- Hohes Drehmoment bei großen Gewindeabmessungen
Fehlervermeidung bei der Verwendung von Gewindeformern
Unsere GARANT Highlight Produkte zum Gewindeformen:
3. Herstellungsverfahren: Gewindefräsen
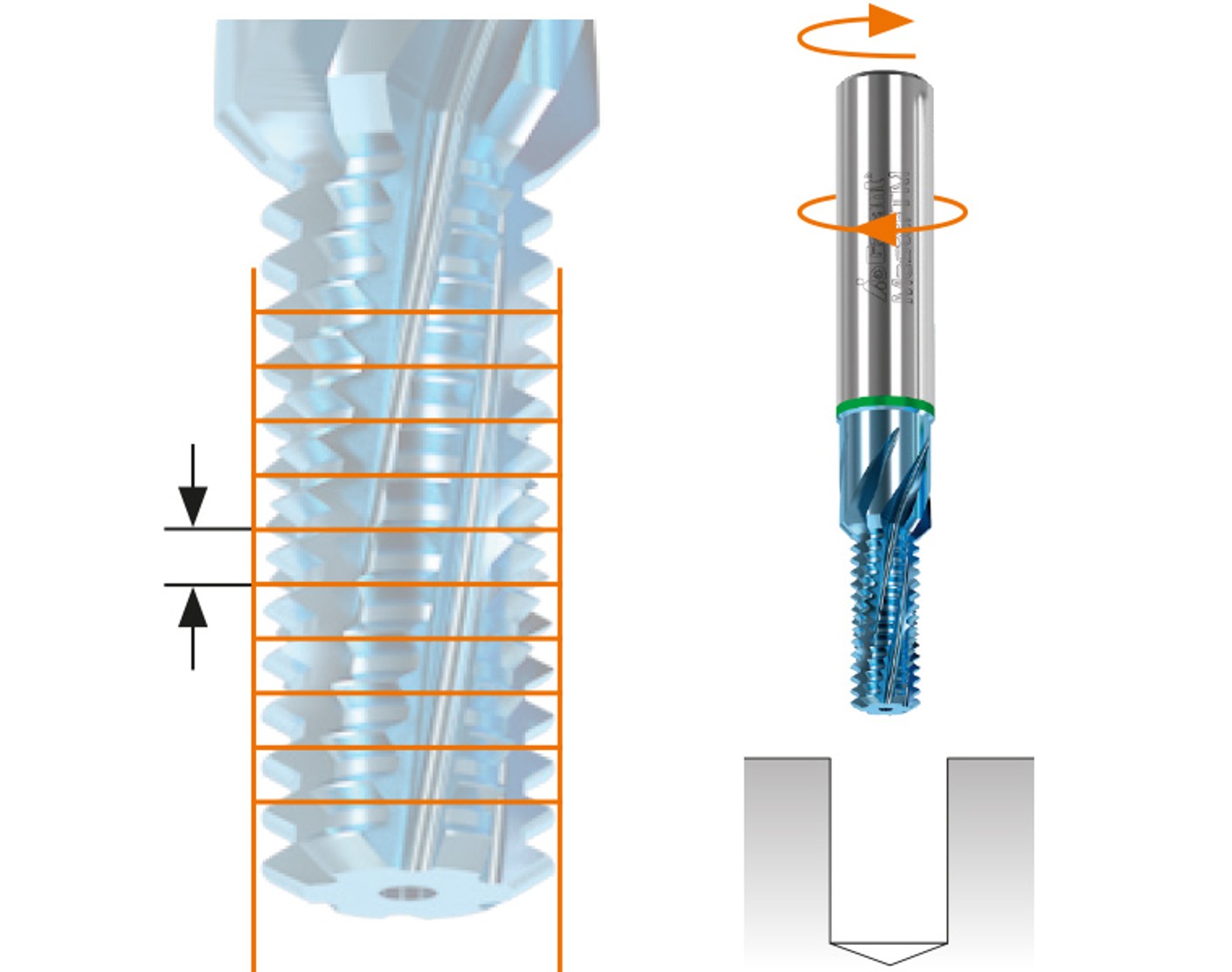
Gewindeherstellung mit kurzen Hauptzeiten:
Voraussetzung für den Einsatz eines Gewindefräsers ist eine 3D-CNC-Steuerung.
Nach der Zustellung auf die Arbeitstiefe taucht zur Belastungsreduzierung das Werkzeug in einer spiralförmigen Bewegung radial in das Werkstück ein. Durch Rotation des Gewindefräsers und gleichzeitiger Bewegung der drei Hauptachsen des BAZ wird nun das Gewinde in einer 360°-Bewegung erzeugt.
Gewindefräser bieten vielfältige Anwendungsmöglichkeiten:
- Gewindefräser können weitgehend universell in unterschiedlichsten Materialien eingesetzt werden.
- Hohe Schnittgeschwindigkeiten und Vorschübe tragen in der Produktion wesentlich zur Zeitersparnis bei.
- Es besteht nicht die Gefahr eines axialen Verschneidens des Gewindes.
- Kurze Frässpäne sind außerdem vorteilhaft für die Prozesssicherheit.
Vor- und Nachteile des Gewindefräsens

Vorteile:
- Sehr universell und flexibel einsetzbar
- Ein Werkzeug für Grund- und Durchgangslochbearbeitung
- Ein Werkzeug für Rechts- und Linksgewinde
- Mit einem Werkzeug verschiedene Toleranzlagen möglich
- Prozesssicher dank kurzer Späne, keine Spänewickler
- Werkzeugbruch führt nicht zum Bauteil-Ausschuss
- Niedriges Drehmoment, auch bei großen Gewindeabmessungen

Nachteile:
- Hohe Werkzeugkosten
- Aufwendige Programmierung und
- Anspruch an Maschine
- Bearbeitungszeit bei Massenfertigung oft unwirtschaftlich
Bearbeitungsstrategien beim Gewindefräsen
Optimierung beim Einsatz von Gewindefräsern
Mit einem Gewindefräser wird im Normalfall das komplette Gewinde in einer 360°-Bewegung gefertigt. Bei besonderen Anforderungen kann eine Schnittkraftaufteilung sinnvoll sein. Auch eine Änderung der Laufrichtung kann das Arbeitsergebnis optimieren.
Werkstückprogrammierung:
- Werkzeugmaschinen arbeiten beim Gewindefräsen meist mit steuerungseigenen Zyklen
- Bei Programmierung der Schnittparameter ist darauf zu achten, ob der Konturvorschub v, oder Mittelpunktbahnvorschub V m vorzugeben ist
- Tipp: Testlauf über dem Werkstück abfahren und Zykluszeit beachten
Schnittkraftaufteilung (Empfehlungen) bei kritischen Fräsoptionen:
- Bei Gewindetiefen >2×D und großen Gewindesteigungen (P>1,5 mm) mit radialer Schnittaufteilung von 2/3 – 1/3 arbeiten
- Bei dünnwandigen Werkstoffen und instabilen Bedingungen
- Bei Problemen mit konischer Gewindeausformung durch Werkzeugabdrängung
- Durch radiale Schnittaufteilung werden Torsionskräfte und Biegemoment deutlich reduziert
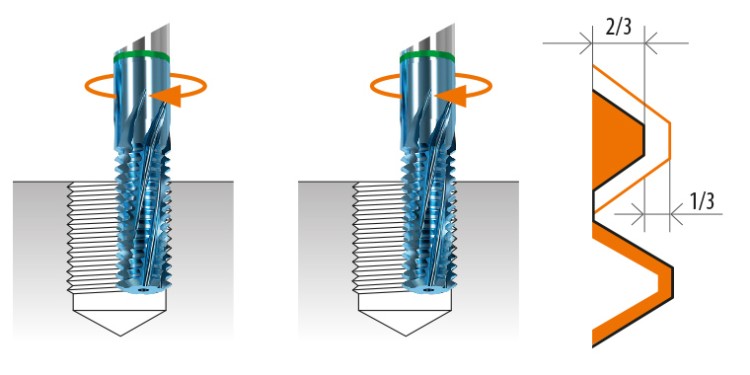
Radiale Schnittaufteilung
Das Gewinde wird zunächst zu ca. 2/3 und danach in einem zweiten Schritt endgültig ausgeformt.

Axiale Schnittaufteilung
Hier wird erst ein Teil des Gewindes hergestellt und dann die gesamte Gewindetiefe bearbeitet.
Wahl der idealen Werkzeugbewegung:
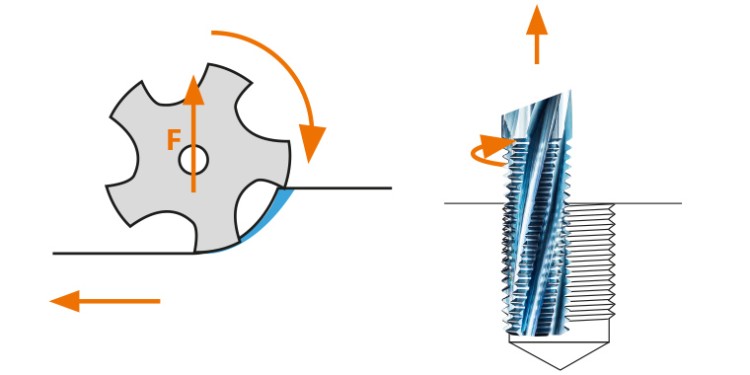
Gleichlauffräsen
Radial-Kraft F wirkt in Richtung Zentrum. Geringe Spandicke bei Schneidenaustritt

Gegenlauffräsen
Radial-Kraft F wirkt in Richtung Werkstück. Höhere Spandicke bei Schneidenaustritt

Vorteile:
- Vibrationen werden reduziert (Rattermarken)
- Verbesserte Werkzeugstandzeiten
- Durch geringen Schnittdruck für dünnwandige Werkstücke

Nachteile:
- Hohe Werkzeugkosten
- Aufwendige Programmierung und
- Anspruch an Maschine
- Bearbeitungszeit bei Massenfertigung oft unwirtschaftlich
Vermeidung von Problemen beim Einsatz von Gewindefräsern
4. Herstellungsverfahren: Bohrzirkulargewindefräsen

Voraussetzung für den Einsatz eines Bohrzirkulargewindefräsers ist ebenfalls wie beim Gewindefräser eine 3D-CNC-Steuerung. Anders als beim Gewindefräsen, taucht der Bohrzirkulargewindefräser mit einer Helixbewegung in das Material ohne Kernlochbohrung ein. Bohren, Gewindefräsen und Fasen ist mit nur einer einzigen Operation möglich.
Bohrzirkulargewindefräser als Problemlöser für unterschiedlichste Ansprüche:
Ein Bohrzirkulargewindefräser steht für Prozesssicherheit, insbesondere bei finalen Bearbeitungsaufgaben an aufwendigen Bauteilen. Er ist hervorragend geeignet, um auf schiefen oder nicht planen Oberflächen ein Gewinde einzubringen.
Ein Verlaufen des Bohrzirkulargewindefräsers aufgrund schräger Gewinde-Ein- und Ausläufern ist ausgeschlossen. Zudem ist er für instabile Aufspannverhältnisse geeignet. Selbst bei schwer zerspanbaren Werkstoffen bis zu 63 HRC bietet dieses Werkzeug eine hervorragende Prozesssicherheit.
Bohrzirkulargewindefräser:
Beim Bohrzirkulargewindefräsprozess sind gewisse Abweichungen bei der Bearbeitungsstrategie zu beachten, welche sich vom Standard Gewindefräsen unterscheiden.
Schnittkraftaufteilung:
Mit einem Bohrzirkulargewindefräser wird das Gewinde mit einem einzigen Bearbeitungszyklus auf Gewindetiefe lehrenhaltig fertig gestellt. Eine Schnittkraftaufteilung ist nicht notwendig, da die auftretenden radialen Kräfte konstant bleiben auch bei unterschiedlichen Gewindetiefen.
Werkzeugeinrichtung:
Mithilfe des angegebenen Programmierradius (RPRG-Wert), welcher am Schaft aufgelasert ist, kann der Anwender beim ersten Gewinde sofort eine lehrenhaltige Gewindebohrung erzeugen.
Strategie:
Der Bohrzirkulargewindefräser ist linksschneidend ausgeführt. Daher erfolgt die Bearbeitung bei Rechtsgewinden somit im Gleichlauf, bei Linksgewinden demnach im Gegenlauf. Die Kühlung mit Druckluft ermöglicht höchste Standmengen in gehärteten Materialien bis zu 63 HRC. Die Gewindeschutzsenkung kann entweder vor dem eigentlichen Gewindefräsprozess erzeugt werden oder danach.
Gewindefräsprozess:
Die Stirnschneidengeometrie erzeugt den Kerndurchmesser des Gewindes. Die Stirnschneide ist so konzipiert, dass beim Erreichen der Gewindetoleranzmitte, der Kernloch-⌀ innerhalb der Kernlochtoleranz liegt. Somit wird die Lehrenhaltigkeit des Kernlochs und zugleich des Gewindes erreicht. Die erste Schneide des Bohrzirkulargewindefräsers dient als Vorschneider des Gewindeprofils. Sie leistet im Gewindefräsprozess die Hauptzerspanungsarbeit des fertigen Gewindeprofils. Die zweite Schneide leistet die Schlichtarbeit. Die Zerspanungsarbeit der dritten Schneide ist sehr gering und dient eher der Säuberung des Gewindes als Leerschnitt.