Tolerance is key – finish machining
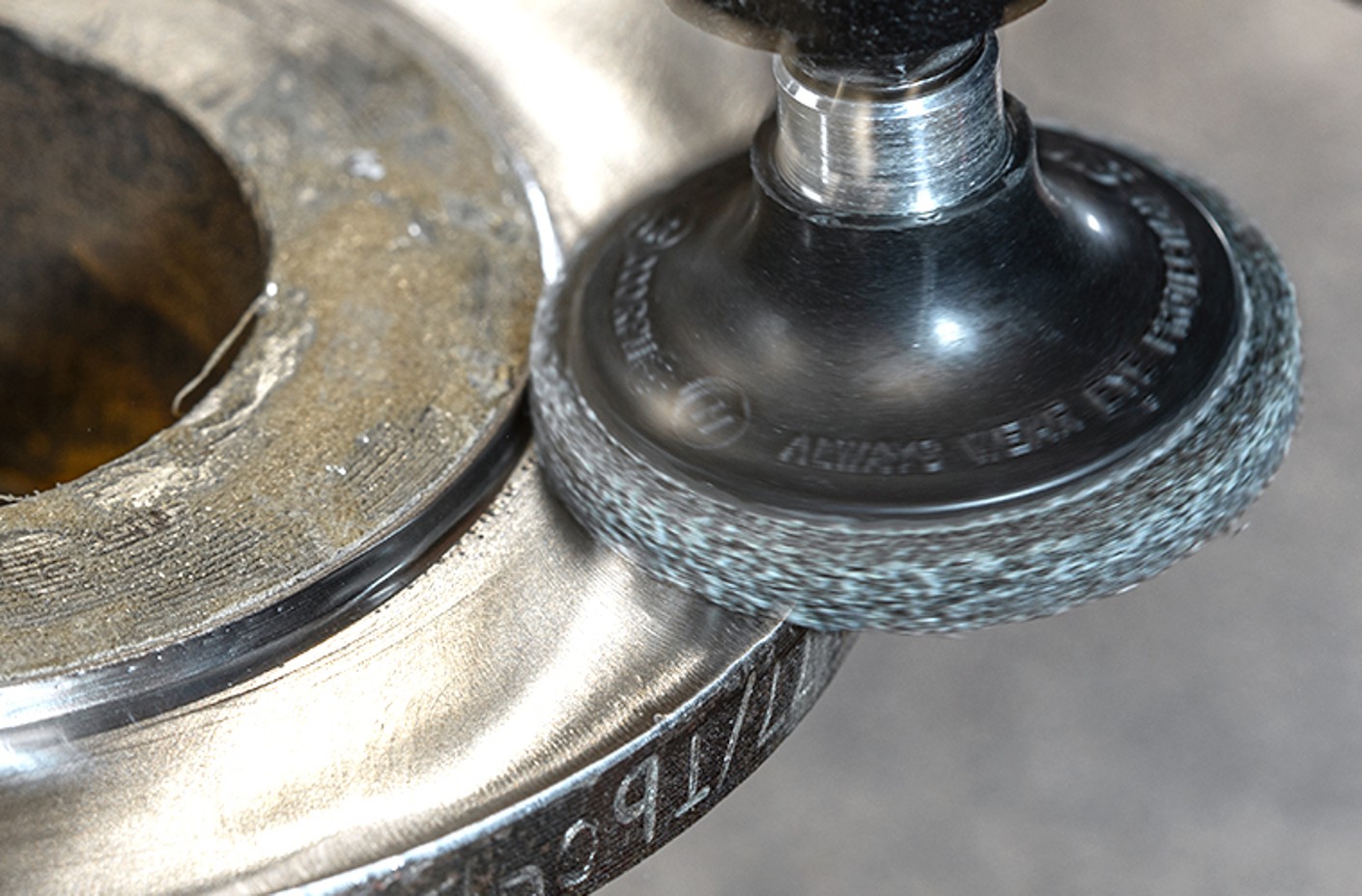
Finish machining is especially unforgiving of mistakes. As a proficient master craftsman, you know how technical requirements in terms of geometrical accuracy, surface quality and of course dimensional tolerance are incredibly demanding to meet today, making the correction of imprecision a true art.
But there’s finish machining and then there’s finish machining. Which of the various methods – etching, honing or grinding for example – you end up choosing depends on the component requirements set by the customer. Other aspects you need to account for, too, are desired surface roughness and tolerance. Find out what the different finish machining methods are, and what they have and don’t have in common. You’ll also learn how to get the most out of different grinding media when finish machining in your workshop.
So fine – your options for component machining
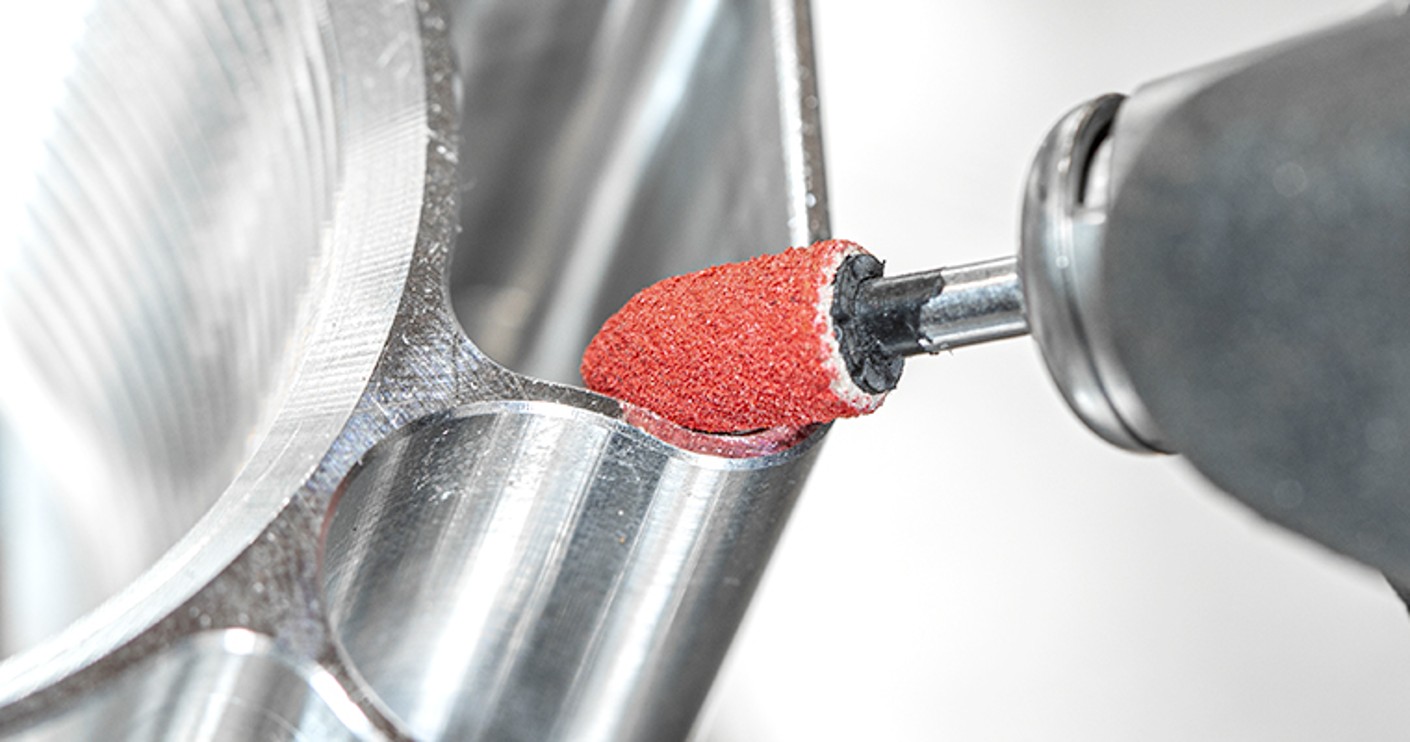
If your jobs today include high-precision finish machining on component surfaces, you’ll need to find out which of the following is best suited for the respective material, component size and shape:
- chemical removal (etching)
- electrochemical removal
- wire-cut electrical discharge machining and die sinking
- hard machining
- high-speed cutting
- honing
- lapping
- ultrasonic lapping
- scraping
- grinding
- vibratory finishing
Etching …
… Method used for example on very small metal parts of thin material. Allows for highly precise contour shaping or surface texturing. Some etching processes allow making very deep but also extremely narrow channels (micrometre range) in metals.
Electrolysis …
… Application that allows removing the minutest of irregularities and burrs, for example from complex 3D shapes. Also used where delicate components need to be protected from mechanical and thermal loads.
Eroding …
… Method for particularly hard metals. Utilises electric discharges between two electrodes (workpiece and tool electrode).
Honing …
… One of the special grinding methods; used on drilled holes and shafts. The method uses a honing tool that simultaneously performs rotating grinding motion and back-and-forth or up-and-down movements to polish a surface.
Lapping …
… The gentlest machining form among the grinding processes, which can be seen from the component’s final surface appearance: lapping does not leave any surface finish marks on metal, instead producing a burnished, uniform surface completely free of furrows. Minute grinding tips are suspended in lapping fluid between a workpiece and the lapping wheel – the disc’s rotation causes material to be removed from the component’s surface. Because mechanical and thermal load is minimal, lapping is considered a cold machining process.
High Speed Cutting …
… Milling method with speeds reaching up to around 8,000 m/min. One of the high-speed method’s focuses is reduced tool wear. It touches on the fields of minimum lubrication and dry machining.
Scraping …
… No longer frequently encountered today, this is a chip-cutting process with geometrically defined blade. Back before lathes and milling machines were able to achieve today’s levels of precision, scraping was used to work races, mating surfaces or oil chambers into sliding surfaces.
Grinding …
… To this day, remains the method of choice in industrial workshops for manual or machine grinding surfaces in preparation for subsequent work or to apply the final finish.

Finesse for component precision
What makes finish machining metals or polymers in industrial environments stand out is that you can achieve dimensional accuracy and precision using machines but also by hand with hones, hand lappers or bench stones. For finish contouring, you can use abrasive sanding sponge or non-woven sanding sheets. This finish grinding medium, usually available in rolls or by the sheet, is really flexible, adopting the component surface’s shape as well as your hand’s when you use it. If you’re looking to apply slightly greater pressure, use a sanding block for good results.
Because making any kind of change to the component’s shape is out of the question, finish machining employs grinding tools that merely smoothen the surface.

Do you need advice in choosing the right grinding media for your finish machining?
Call us now, our experts will talk you through the grinding media best suited to your specific needs.